Drills & Screwdrivers Bosch
All models Advanced filters → |
You might be interested in
Articles, reviews, useful tips
All materials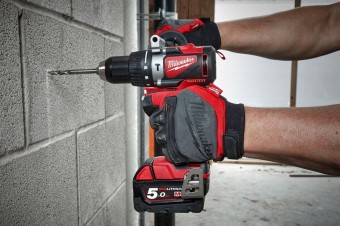
Screwdriver that can drill concrete: myth or reality
What does it take to drill a hole in the wall with a screwdriver? Which model should I choose for drilling concrete?
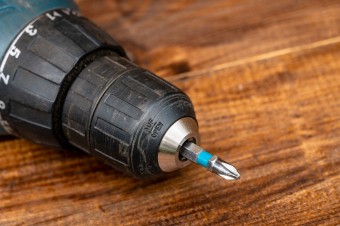
Sparks, smoke, crunch and burning smell: what can break in a drill or screwdriver
We understand why drills and screwdrivers smoke, spew sparks, overheat, make strange sounds and work poorly

What to give dad?
Ideas for practical and useful gifts for father
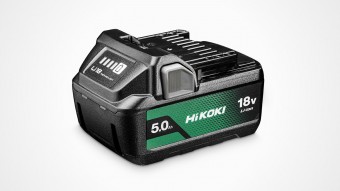
Proper storage methods for power tool batteries
Conditions under which batteries will not lose capacity during extended storage
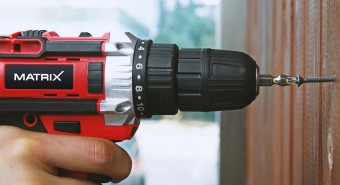
What is torque and why is it important for a tool?
Let's deal with one of the most important features of screwdrivers and impact wrenches
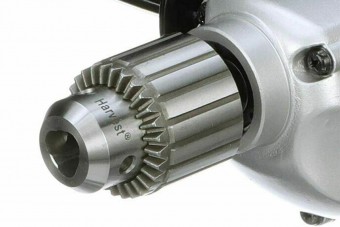
Drill chuck: types and differences
Specifics of different types of chucks for drilling and working with fasteners
Drills & Screwdrivers: specifications, types
Show all
Product type
General type of instrument.
Nowadays, several other types of hand tools are also combined into one category with traditional drills, with a similar design and principle of operation: drill drivers, classic screwdrivers, wrenches and electric screwdrivers. Here is a detailed description of each of these varieties:
— Drill. Traditional drills are power tools for drilling holes in various materials. By specialization and “weight category”, such tools range from miniature cordless models to heavy professional diamond drilling units (see “Intended Use”). Anyway, drills are equipped with chucks for installing drills, as well as engines designed for significant resistance during operation. Also note that many of these units have an impact mode, but the drill is still not able to replace a full-fledged rotary hammer (for more details, see "Functions").
— Screwdriver. In fact, it is an electric (or pneumatic) analogue of a manual screwdriver. It is used primarily for tightening and loosening screws, screws and other similar fasteners using bits — interchangeable nozzles, the shape of which imitates various screwdriver tips (straight, cross-shaped, etc.). Accordingly, the standard type of retainer for the nozzle in such a tool is for a bit (see "Chuck Type"). Screwdrivers differ from electric...screwdrivers (see below) in higher power, better suitability for long-term work and high loads, as well as larger dimensions and rather significant (in comparison, of course) weight.
— Drill driver. Tools (mainly cordless, see "Power source") that combine the functionality of a drill and a screwdriver. See above for more on both, and these "hybrid" devices are extremely popular these days due to their versatility. Switching between drilling and twisting modes in them is carried out by changing the cartridge, and also, in most models, by adjusting the torque (see below). At the same time, it should be noted that compared to traditional drills, the efficiency of such units when drilling is rather low, they are not intended for high loads, hard materials and large drilling diameters. This is due to the fact that in order to achieve high power, it would be necessary to increase the dimensions and weight, which would significantly complicate the use in the format of a screwdriver.
— Screwdriver. A kind of electric and pneumatic analogues of socket wrenches: tools designed to work with nuts and other similar fasteners (for example, bolts with heads without a slot). Nutrunners are in many ways similar to the screwdrivers described above and differ mainly in the type of cartridge — usually it is a square for sockets of different sizes.
— Screwdriver. An electrical analogue of a conventional manual screwdriver (pneumatic drive is not used in such devices for a number of reasons). Some of these models have a straight body shape (see "Construction") and are very similar in appearance to hand tools; others resemble smaller and lighter screwdrivers (see below). Anyway, electric screwdrivers are intended mainly for work where accuracy and accuracy are more important than high efforts (or where these efforts are simply not required). Thus, the low power of such devices is not so much a disadvantage as a feature. In addition, this feature allows you to use battery power without much difficulty, making the tool as autonomous as possible; in fact, electric screwdrivers with mains operation nowadays are almost never found. And the small size and weight, in turn, contribute to the mentioned accuracy and accuracy.
Nowadays, several other types of hand tools are also combined into one category with traditional drills, with a similar design and principle of operation: drill drivers, classic screwdrivers, wrenches and electric screwdrivers. Here is a detailed description of each of these varieties:
— Drill. Traditional drills are power tools for drilling holes in various materials. By specialization and “weight category”, such tools range from miniature cordless models to heavy professional diamond drilling units (see “Intended Use”). Anyway, drills are equipped with chucks for installing drills, as well as engines designed for significant resistance during operation. Also note that many of these units have an impact mode, but the drill is still not able to replace a full-fledged rotary hammer (for more details, see "Functions").
— Screwdriver. In fact, it is an electric (or pneumatic) analogue of a manual screwdriver. It is used primarily for tightening and loosening screws, screws and other similar fasteners using bits — interchangeable nozzles, the shape of which imitates various screwdriver tips (straight, cross-shaped, etc.). Accordingly, the standard type of retainer for the nozzle in such a tool is for a bit (see "Chuck Type"). Screwdrivers differ from electric...screwdrivers (see below) in higher power, better suitability for long-term work and high loads, as well as larger dimensions and rather significant (in comparison, of course) weight.
— Drill driver. Tools (mainly cordless, see "Power source") that combine the functionality of a drill and a screwdriver. See above for more on both, and these "hybrid" devices are extremely popular these days due to their versatility. Switching between drilling and twisting modes in them is carried out by changing the cartridge, and also, in most models, by adjusting the torque (see below). At the same time, it should be noted that compared to traditional drills, the efficiency of such units when drilling is rather low, they are not intended for high loads, hard materials and large drilling diameters. This is due to the fact that in order to achieve high power, it would be necessary to increase the dimensions and weight, which would significantly complicate the use in the format of a screwdriver.
— Screwdriver. A kind of electric and pneumatic analogues of socket wrenches: tools designed to work with nuts and other similar fasteners (for example, bolts with heads without a slot). Nutrunners are in many ways similar to the screwdrivers described above and differ mainly in the type of cartridge — usually it is a square for sockets of different sizes.
— Screwdriver. An electrical analogue of a conventional manual screwdriver (pneumatic drive is not used in such devices for a number of reasons). Some of these models have a straight body shape (see "Construction") and are very similar in appearance to hand tools; others resemble smaller and lighter screwdrivers (see below). Anyway, electric screwdrivers are intended mainly for work where accuracy and accuracy are more important than high efforts (or where these efforts are simply not required). Thus, the low power of such devices is not so much a disadvantage as a feature. In addition, this feature allows you to use battery power without much difficulty, making the tool as autonomous as possible; in fact, electric screwdrivers with mains operation nowadays are almost never found. And the small size and weight, in turn, contribute to the mentioned accuracy and accuracy.
Design
Design describes the overall layout of the tool.
Nowadays, among drills and screwdrivers, you can find models with a pistol, angle, straight, combined pistol-angle, as well as an adjustable design. Here is a more detailed description of each option:
— Pistol. In models with this layout, the handle is perpendicular or almost perpendicular to the body, so that the tool is held in the hands similar to a pistol — hence the name. In general, the pistol design combines convenience, safety, practicality and low cost. Due to this, this option is the most common nowadays, it is widely used in all types of drills and similar tools (see "Device"). In fact, this is a traditional design for such units; other types of layout are used mainly in models designed for special conditions and/or with specific characteristics (see below for more details).
— Corner. The general shape of such tools resembles the letter G: a straight body of relatively large length, which also acts as a handle, and a cartridge bent 90 ° relative to the body. This design option is especially convenient when working in cramped conditions: with the help of an angled tool, you can get into narrow gaps that are inaccessible to traditional pistol-mounted units. On the other hand, the angular layout degrades accuracy somewhat;...it is also poorly suited for jobs that require strong pressure along the axis of rotation of the chuck.
— Direct. Tools of this design have an oblong body, part of which plays the role of a handle; and the axis of rotation of the cartridge in them coincides with the longitudinal axis of the body. This option can be found in two types of tools. The first is small low-power tools (mainly screwdrivers, screwdrivers and wrenches, as well as single models of drills, also characterized by low power). In such cases, a straight body is provided primarily for compactness — a pistol grip would increase the dimensions beyond reasonable limits. The second type of direct units is, on the contrary, separate professional drills with a diamond drilling function (see "Purpose"). Such drills are not designed to be held in hands and are used only with a stand (see "Complete set"); for this format of use, the direct layout is also optimal.
— Pistol / angle. In fact, they are tools of the pistol layout described above, which are supplied with an angular cartridge that allows you to turn the working nozzle 90 ° relative to the standard position. Thus, such models combine the capabilities of both layouts, while retaining the main advantages of a pistol design — convenience and reliability in holding. On the other hand, additional equipment affects the cost, and such versatility is not often required. So this option is not very popular.
— Adjustable. This category includes all models in which you can change the location of the cartridge and/or handle relative to the body. The most popular version of this design is the rotary handle, which allows you to switch the tool from a pistol format to a straight one and vice versa. See above for more on these types of construction, but here we note that the pistol layout is more reliable in holding and versatile, and the straight one is better suited for some delicate work and hard-to-reach places. It is also worth mentioning that the possibilities for adjusting the handle can be different: in some models it has only two extreme positions, in others you can choose the angle of inclination relative to the body. The second, somewhat less common variety of adjustable tools is devices with a rotary chuck. Here we are already talking about switching between a straight and an angular layout — the latter, we recall, is very appropriate when working in cramped conditions. However, the cartridge in such units, usually, can be installed not only at 90 ° relative to the body, but also in several intermediate positions. This further expands the customization options for the specifics of the situation.
Anyway, all adjustable tools are more versatile than non-adjustable ones, but they are more complex in design and less reliable. Therefore, this type of arrangement is found exclusively in low-power units, mainly battery ones (see "Power supply").
Nowadays, among drills and screwdrivers, you can find models with a pistol, angle, straight, combined pistol-angle, as well as an adjustable design. Here is a more detailed description of each option:
— Pistol. In models with this layout, the handle is perpendicular or almost perpendicular to the body, so that the tool is held in the hands similar to a pistol — hence the name. In general, the pistol design combines convenience, safety, practicality and low cost. Due to this, this option is the most common nowadays, it is widely used in all types of drills and similar tools (see "Device"). In fact, this is a traditional design for such units; other types of layout are used mainly in models designed for special conditions and/or with specific characteristics (see below for more details).
— Corner. The general shape of such tools resembles the letter G: a straight body of relatively large length, which also acts as a handle, and a cartridge bent 90 ° relative to the body. This design option is especially convenient when working in cramped conditions: with the help of an angled tool, you can get into narrow gaps that are inaccessible to traditional pistol-mounted units. On the other hand, the angular layout degrades accuracy somewhat;...it is also poorly suited for jobs that require strong pressure along the axis of rotation of the chuck.
— Direct. Tools of this design have an oblong body, part of which plays the role of a handle; and the axis of rotation of the cartridge in them coincides with the longitudinal axis of the body. This option can be found in two types of tools. The first is small low-power tools (mainly screwdrivers, screwdrivers and wrenches, as well as single models of drills, also characterized by low power). In such cases, a straight body is provided primarily for compactness — a pistol grip would increase the dimensions beyond reasonable limits. The second type of direct units is, on the contrary, separate professional drills with a diamond drilling function (see "Purpose"). Such drills are not designed to be held in hands and are used only with a stand (see "Complete set"); for this format of use, the direct layout is also optimal.
— Pistol / angle. In fact, they are tools of the pistol layout described above, which are supplied with an angular cartridge that allows you to turn the working nozzle 90 ° relative to the standard position. Thus, such models combine the capabilities of both layouts, while retaining the main advantages of a pistol design — convenience and reliability in holding. On the other hand, additional equipment affects the cost, and such versatility is not often required. So this option is not very popular.
— Adjustable. This category includes all models in which you can change the location of the cartridge and/or handle relative to the body. The most popular version of this design is the rotary handle, which allows you to switch the tool from a pistol format to a straight one and vice versa. See above for more on these types of construction, but here we note that the pistol layout is more reliable in holding and versatile, and the straight one is better suited for some delicate work and hard-to-reach places. It is also worth mentioning that the possibilities for adjusting the handle can be different: in some models it has only two extreme positions, in others you can choose the angle of inclination relative to the body. The second, somewhat less common variety of adjustable tools is devices with a rotary chuck. Here we are already talking about switching between a straight and an angular layout — the latter, we recall, is very appropriate when working in cramped conditions. However, the cartridge in such units, usually, can be installed not only at 90 ° relative to the body, but also in several intermediate positions. This further expands the customization options for the specifics of the situation.
Anyway, all adjustable tools are more versatile than non-adjustable ones, but they are more complex in design and less reliable. Therefore, this type of arrangement is found exclusively in low-power units, mainly battery ones (see "Power supply").
Suitable for
Specific purpose of the tool.
This parameter is specified if the device has a specialization that significantly distinguishes it from the same type of general-purpose tools. It can be either a core specialization that defines all application options (an example is diamond drilling), or an additional functionality that expands general capabilities (an example is threading). Here is a more detailed description of today's most relevant appointments:
— For diamond drilling. Diamond drilling(mainly with crowns) is used for materials of high hardness, which are not able to cope with conventional nozzles. Accordingly, the main features of a tool that allows such use are high power and the ability to carry significant loads. In addition, many (though not all) drills with this specialization are equipped with a stand (see below), a threaded spindle rather than a chuck is usually used to mount bits (see "Chuck Type"), and additional features often include water cooling. .
— For drywall. Specialization, found mainly in screwdrivers (see "Device"). One of the mandatory features for a tool with this purpose is a depth gauge — it reduces the risk of damaging a rather delicate material, which is drywall. In addition, when working with drywall, it is often necessary to tighten the fasteners “quickly and in large quantities”, and to speed up the work, the screwdriver can be equipped with a special...magazine nozzle; for more details, see "Complete set".
— For cutting threads. A feature found in some relatively low-powered tools, predominantly in the drill/driver format. For this, a special mode of operation is provided: first, the cartridge with the appropriate nozzle (die or tap) rotates clockwise, cutting the thread, and then in the opposite direction to remove / extract the nozzle. In addition, on the return stroke, the teeth of the nozzle pass over fresh cuts, clearing them of chips.
— For precision work. A tool originally designed for jobs that require precision and precision. Most of these models are screwdrivers (see "Device"), which have a very thin and light body that is comfortable to hold in your hand and allows you to make the most accurate movements. Note that the downside of this convenience is very low power; in fact, for more than "fine" work, such a tool is usually not designed.
— Automotive. A tool designed for use in a car — both for repairing the car itself (for example, changing a wheel), and for other work in the "field conditions", where the most convenient (or even the only available) power source is the car's on-board network. Accordingly, all car models have the ability to connect to such a network — usually through a standard cigarette lighter socket, although terminals for working directly from the battery can be supplied in the kit. And some automotive tools come with their own batteries; see "Food" for details.
— For spot welding. A specific type of drill designed for drilling connection points between spot welded parts. Such drills are especially popular in a car service — it is there that it often becomes necessary to remove a separate part welded “by points”, and the easiest way to do this is by drilling individual points. The specificity of such work lies in the fact that the junction cannot be drilled through — the working nozzle (drill or crown) must pass only through the upper layer of metal, almost without affecting the lower one. This means that the depth of drilling must be controlled very precisely. To do this, special limiters are used in spot welding drills, which look like clamps and allow you to set the drilling depth with an accuracy of fractions of a millimetre.
This parameter is specified if the device has a specialization that significantly distinguishes it from the same type of general-purpose tools. It can be either a core specialization that defines all application options (an example is diamond drilling), or an additional functionality that expands general capabilities (an example is threading). Here is a more detailed description of today's most relevant appointments:
— For diamond drilling. Diamond drilling(mainly with crowns) is used for materials of high hardness, which are not able to cope with conventional nozzles. Accordingly, the main features of a tool that allows such use are high power and the ability to carry significant loads. In addition, many (though not all) drills with this specialization are equipped with a stand (see below), a threaded spindle rather than a chuck is usually used to mount bits (see "Chuck Type"), and additional features often include water cooling. .
— For drywall. Specialization, found mainly in screwdrivers (see "Device"). One of the mandatory features for a tool with this purpose is a depth gauge — it reduces the risk of damaging a rather delicate material, which is drywall. In addition, when working with drywall, it is often necessary to tighten the fasteners “quickly and in large quantities”, and to speed up the work, the screwdriver can be equipped with a special...magazine nozzle; for more details, see "Complete set".
— For cutting threads. A feature found in some relatively low-powered tools, predominantly in the drill/driver format. For this, a special mode of operation is provided: first, the cartridge with the appropriate nozzle (die or tap) rotates clockwise, cutting the thread, and then in the opposite direction to remove / extract the nozzle. In addition, on the return stroke, the teeth of the nozzle pass over fresh cuts, clearing them of chips.
— For precision work. A tool originally designed for jobs that require precision and precision. Most of these models are screwdrivers (see "Device"), which have a very thin and light body that is comfortable to hold in your hand and allows you to make the most accurate movements. Note that the downside of this convenience is very low power; in fact, for more than "fine" work, such a tool is usually not designed.
— Automotive. A tool designed for use in a car — both for repairing the car itself (for example, changing a wheel), and for other work in the "field conditions", where the most convenient (or even the only available) power source is the car's on-board network. Accordingly, all car models have the ability to connect to such a network — usually through a standard cigarette lighter socket, although terminals for working directly from the battery can be supplied in the kit. And some automotive tools come with their own batteries; see "Food" for details.
— For spot welding. A specific type of drill designed for drilling connection points between spot welded parts. Such drills are especially popular in a car service — it is there that it often becomes necessary to remove a separate part welded “by points”, and the easiest way to do this is by drilling individual points. The specificity of such work lies in the fact that the junction cannot be drilled through — the working nozzle (drill or crown) must pass only through the upper layer of metal, almost without affecting the lower one. This means that the depth of drilling must be controlled very precisely. To do this, special limiters are used in spot welding drills, which look like clamps and allow you to set the drilling depth with an accuracy of fractions of a millimetre.
Real power
The useful power of the tool is the maximum power that it can deliver to the working nozzle. This power is always less than the power consumed (see below), since part of the electricity inevitably goes to heat and friction in the tool mechanisms. In addition, this parameter is not given for every model, often information in the characteristics is limited to power consumption. Nevertheless, the actual capabilities of the tool directly depend on the net power: the higher it is, the greater the speed and/or torque this model is able to develop, the easier it is for it to cope with tasks that require high efforts. So, to compare different devices with each other, it is best to use this parameter (of course, you can only compare models of the same type or similar in type).
Also note that high working power is not always an advantage: it accordingly affects the dimensions, weight and price of the tool, while in fact high speeds and efforts are not always necessary. Detailed recommendations on the optimal values for different tools and different types of work can be found in special sources.
Also note that high working power is not always an advantage: it accordingly affects the dimensions, weight and price of the tool, while in fact high speeds and efforts are not always necessary. Detailed recommendations on the optimal values for different tools and different types of work can be found in special sources.
Power consumption
The total power consumed by a mains-powered electric tool (see "Power Source"). It is considered the main criterion for assessing the overall capabilities of a particular model: more power allows you to achieve more speed and/or torque. However a more correct parameter for such an assessment is useful (working) power, but it is far from always indicated, and tools of the same type with similar power consumption usually do not differ much in terms of working power. In addition, data on power consumption also allows you to estimate the load on the power grid or other power source; in some cases this is unnecessary.
As for specific figures, for different types of tools, the characteristic power values will be different. For example, from 750 to 1000 W is considered a very solid indicator for a screwdriver, while for classic drills this is an average value, among such devices there are options even for 1.5 kW or more. Detailed recommendations on choosing a tool for this parameter can be found in special sources. We only note that it does not always make sense to chase the maximum values high power noticeably affects the dimensions, weight and price of the unit, despite the fact that it is far from always required.
As for specific figures, for different types of tools, the characteristic power values will be different. For example, from 750 to 1000 W is considered a very solid indicator for a screwdriver, while for classic drills this is an average value, among such devices there are options even for 1.5 kW or more. Detailed recommendations on choosing a tool for this parameter can be found in special sources. We only note that it does not always make sense to chase the maximum values high power noticeably affects the dimensions, weight and price of the unit, despite the fact that it is far from always required.
Rated pressure
Nominal air pressure for a tool powered by a compressor (see "Power Source"). This is the optimal value, the one for which the device was originally designed. The actual performance of the connected compressor may differ, but this is undesirable: if the pressure is too high, the tool will experience off-design loads and may fail (and in the worst case, even injure the user), and if the pressure is too low, it will not be able to produce power, necessary for normal operation.
Rotation speed
The speed of rotation of the working nozzle provided by the tool.
If a single number is indicated in this paragraph (for example, 1800), it can be either a standard, constant, or maximum rotation speed. This refers to the maximum speed if the tool has more than one speed (see "Number of speeds") and/or a speed controller (see "Functions"). In turn, two or three numbers through an oblique line (for example, 1100/2300/3400) are indicated only for models that have the corresponding number of individual speeds. Each of these numbers indicates the standard (and in the presence of a speed controller — the maximum) number of revolutions at one of the speeds.
Anyway, when choosing a tool by the number of revolutions, it is worth considering both its general type (see "Device") and the specifics of the intended work. Detailed recommendations on this matter are quite extensive, it makes no sense to give them in full here — it is better to turn to special sources. We note only a few general points. So, high -speed drills nowadays are considered to be drills capable of delivering more than 3000 rpm. In general, high speed contributes to productivity, but there is also a downside: increasing the speed (for the same power) reduces torque — accordingly, the efficiency of working with stubborn materials and large diameter nozzles decreases. Therefore, it makes sense to specifically look for a "high-speed" tool only if speed is of key impor...tance; it doesn’t hurt to make sure that the model you choose can provide the required efficiency and torque.
If a single number is indicated in this paragraph (for example, 1800), it can be either a standard, constant, or maximum rotation speed. This refers to the maximum speed if the tool has more than one speed (see "Number of speeds") and/or a speed controller (see "Functions"). In turn, two or three numbers through an oblique line (for example, 1100/2300/3400) are indicated only for models that have the corresponding number of individual speeds. Each of these numbers indicates the standard (and in the presence of a speed controller — the maximum) number of revolutions at one of the speeds.
Anyway, when choosing a tool by the number of revolutions, it is worth considering both its general type (see "Device") and the specifics of the intended work. Detailed recommendations on this matter are quite extensive, it makes no sense to give them in full here — it is better to turn to special sources. We note only a few general points. So, high -speed drills nowadays are considered to be drills capable of delivering more than 3000 rpm. In general, high speed contributes to productivity, but there is also a downside: increasing the speed (for the same power) reduces torque — accordingly, the efficiency of working with stubborn materials and large diameter nozzles decreases. Therefore, it makes sense to specifically look for a "high-speed" tool only if speed is of key impor...tance; it doesn’t hurt to make sure that the model you choose can provide the required efficiency and torque.
Max. beats
The number of beats per minute provided by a tool that supports the corresponding mode.
For more information about this mode, see "Functions", here we note that it can be provided both in drills and in screwdrivers and wrenches (see "Device"), and the meaning of the impact mode in these varieties is somewhat different. Therefore, the speeds differ: many drills are capable of delivering about 48,000 beats / min, or even 64,000 beats / min, while in screwdrivers and wrenches, 3200 beats / min are considered “classics of the genre”, and values above 3500 beats / min are practically do not meet.
The general meaning of this indicator is also directly related to the type. So, among drills, the difference in chiseling speed can be quite large. With these tools, more strokes improve overall productivity and efficiency, while fewer strokes improve accuracy and reduce the risk of damaging delicate materials. In screwdrivers and nutrunners, high speed also contributes to overall efficiency, but for most of these tools, the differences in this indicator are not significant enough to be noticeable in practice.
For more information about this mode, see "Functions", here we note that it can be provided both in drills and in screwdrivers and wrenches (see "Device"), and the meaning of the impact mode in these varieties is somewhat different. Therefore, the speeds differ: many drills are capable of delivering about 48,000 beats / min, or even 64,000 beats / min, while in screwdrivers and wrenches, 3200 beats / min are considered “classics of the genre”, and values above 3500 beats / min are practically do not meet.
The general meaning of this indicator is also directly related to the type. So, among drills, the difference in chiseling speed can be quite large. With these tools, more strokes improve overall productivity and efficiency, while fewer strokes improve accuracy and reduce the risk of damaging delicate materials. In screwdrivers and nutrunners, high speed also contributes to overall efficiency, but for most of these tools, the differences in this indicator are not significant enough to be noticeable in practice.
Torque
Torque is the maximum force with which this model is capable of turning the working nozzle.
Higher torque gives more options, it allows you to cope with complex tasks such as drilling in hard materials, unscrewing stuck screws and nuts, etc. On the other hand, a lot of force requires corresponding power — and this, in turn, affects the dimensions , weight and cost of the tool itself, and also puts forward increased power requirements (mains power, battery capacity or pressure / compressor performance). And for some tasks, excessive torque is basically unacceptable, so for maximum versatility, it is desirable to have torque control — and this affects the cost even more. And the more steps, the more optimally you can configure the tool to perform a particular type of work. So the general rule is this: when choosing, it is worth considering the specifics of the planned work, and not chasing the greatest working effort.
Detailed recommendations on choosing the optimal torque for different types of tools (see "Device") can be found in special sources. Here we note that it is of key importance primarily for screwdrivers, although it is also given for other types of tools. At the same time, in the “weakest” models, the maximum working force does not exceed 15 Nm, in the most powerful ones it is more than 150 Nm.
Higher torque gives more options, it allows you to cope with complex tasks such as drilling in hard materials, unscrewing stuck screws and nuts, etc. On the other hand, a lot of force requires corresponding power — and this, in turn, affects the dimensions , weight and cost of the tool itself, and also puts forward increased power requirements (mains power, battery capacity or pressure / compressor performance). And for some tasks, excessive torque is basically unacceptable, so for maximum versatility, it is desirable to have torque control — and this affects the cost even more. And the more steps, the more optimally you can configure the tool to perform a particular type of work. So the general rule is this: when choosing, it is worth considering the specifics of the planned work, and not chasing the greatest working effort.
Detailed recommendations on choosing the optimal torque for different types of tools (see "Device") can be found in special sources. Here we note that it is of key importance primarily for screwdrivers, although it is also given for other types of tools. At the same time, in the “weakest” models, the maximum working force does not exceed 15 Nm, in the most powerful ones it is more than 150 Nm.
Reducer
The type of gearbox provided in the design of the tool.
A gearbox can be simply described as a mechanism that transmits rotation from an electric motor to a chuck. In this case, usually, the rotation speed decreases, due to which the torque increases. Different types of gearboxes differ just in the number of speeds that can be obtained at the output. The simplest variety of such mechanisms is single-speed, they are as simple as possible, compact and reliable. At the same time, in a tool with a 1-speed gearbox, speed control may well be provided — due to electronic circuits that allow you to adjust the engine speed. On the other hand, reducing the actual speed by means of electronic control does not lead to an increase, but to a decrease in torque.
More advanced are multi-speed gearboxes, usually having 2 to 4 speeds. Such mechanisms are analogous to a gearbox in a car: the speed in them is regulated by changing the gear ratio, so that a decrease in speed leads to an increase in torque, and vice versa. Such an adjustment is considered more practical than the electronic one described above; the downside is the complexity and high cost of multi-speed gearboxes.
A gearbox can be simply described as a mechanism that transmits rotation from an electric motor to a chuck. In this case, usually, the rotation speed decreases, due to which the torque increases. Different types of gearboxes differ just in the number of speeds that can be obtained at the output. The simplest variety of such mechanisms is single-speed, they are as simple as possible, compact and reliable. At the same time, in a tool with a 1-speed gearbox, speed control may well be provided — due to electronic circuits that allow you to adjust the engine speed. On the other hand, reducing the actual speed by means of electronic control does not lead to an increase, but to a decrease in torque.
More advanced are multi-speed gearboxes, usually having 2 to 4 speeds. Such mechanisms are analogous to a gearbox in a car: the speed in them is regulated by changing the gear ratio, so that a decrease in speed leads to an increase in torque, and vice versa. Such an adjustment is considered more practical than the electronic one described above; the downside is the complexity and high cost of multi-speed gearboxes.
Number of speeds
The number of speeds provided in the design of the tool.
First of all, let's clarify that "speed" in this case means high-speed mode. The number of revolutions at each "speed" can be either fixed or adjustable (if there is an appropriate regulator — see "Functions"). Thus, the presence of several speeds can have different meanings. In some models, changing the speed mode is the only option for adjusting the speed; in others (if there is a separate speed controller), changing the mode sets only the maximum speed of rotation of the nozzle, and its actual speed is smoothly changed by the controller (which may also have its own, additional speed limiter).
As for the specific number of speed modes, in many models it is only one. Accordingly, the revolutions in such a tool either do not change at all, or are controlled only by the mentioned regulator; this is often sufficient for simple tasks. However, 2-speed tools are also very widespread — this design provides additional tuning options and at the same time remains relatively simple and inexpensive. And in fairly advanced models, you can find three, or even four or more speed modes; in some cases, this number reaches 8 or even more, which allows you to use speed switching as a full-fledged speed controller.
When choosing according to this characteristic, it should be...taken into account that, other things being equal, a larger number of speeds gives more features for setting operating parameters, but complicates the design and increases its cost.
First of all, let's clarify that "speed" in this case means high-speed mode. The number of revolutions at each "speed" can be either fixed or adjustable (if there is an appropriate regulator — see "Functions"). Thus, the presence of several speeds can have different meanings. In some models, changing the speed mode is the only option for adjusting the speed; in others (if there is a separate speed controller), changing the mode sets only the maximum speed of rotation of the nozzle, and its actual speed is smoothly changed by the controller (which may also have its own, additional speed limiter).
As for the specific number of speed modes, in many models it is only one. Accordingly, the revolutions in such a tool either do not change at all, or are controlled only by the mentioned regulator; this is often sufficient for simple tasks. However, 2-speed tools are also very widespread — this design provides additional tuning options and at the same time remains relatively simple and inexpensive. And in fairly advanced models, you can find three, or even four or more speed modes; in some cases, this number reaches 8 or even more, which allows you to use speed switching as a full-fledged speed controller.
When choosing according to this characteristic, it should be...taken into account that, other things being equal, a larger number of speeds gives more features for setting operating parameters, but complicates the design and increases its cost.
Reverse
Type of reverse provided in the design of the tool.
The reverse allows you to switch the direction of rotation of the nozzle; see "Functions" for details. It also indicates the type of switch responsible for this function. The varieties of such switches nowadays are very diverse: slider, flag, brush on the engine, on the start button, gyroscopic, on the keyboard toggle switch, and also combined with a flow switch or ratchet mechanism. Here is a detailed description of each of these varieties:
— Crawler. Switch in the form of a slider with two opposite positions. Usually, it moves in the direction "back and forth" relative to the tool chuck — this format is considered the most practical. The sliders are quite simple and at the same time convenient and visual, especially when used in screwdrivers and wrenches: by moving forward (away from you), the direction of rotation is set to twisting, by moving backward (toward yourself), respectively, to unscrewing. However, such devices are widely used in other types of instruments (see "Device") and are generally the most popular option nowadays.
— Combined with the flow switch. The most popular type of reve...rse in pneumatic tools (see "Power Source"); not found in other models. The flow switch itself is actually a speed controller, most often in the form of a distinctive rotary knob or lever. And if this regulator is combined with a reverse, this means that it can deviate from the neutral position in two directions, and the direction of rotation will depend on which direction the flow switch is shifted.
— Flag. A switch in the form of a flag, usually installed above the start button and thrown to the right and left. One of the advantages of a checkbox is that it is right at your fingertips and can be toggled with almost no unnecessary movement (which is not always available for a slider). On the other hand, this option is mainly suitable for drills, and in screwdrivers and wrenches, the checkbox is not as intuitive as the same slider. And in general, this type of reverse for a number of reasons is much less common.
— Brush (on the engine). Reverse switch installed directly in the tool motor and based on the use of a special movable brush holder. By changing the position of the brushes in the motor with the help of such a mechanism, it is possible to change the direction of its rotation. One of the key advantages of this method is that it allows you to achieve maximum power in any direction of rotation without any special tricks. In addition, such an adjustment has a positive effect on the engine resource. On the other hand, brush switches are quite complex and expensive, and therefore are installed mainly in a powerful professional tool.
— On the start button. Reverse switch combined with start button. Such a combination button is usually made in the form of a "rocker", and the direction of rotation depends on which side of the rocker the user pressed; pressing the same button immediately starts the engine. This design allows you to easily and quickly change the direction of rotation — for this you do not need to be distracted by individual switches, just move your finger slightly and press the other half of the start button. This is especially convenient for screw and wrench drivers, as well as screwdrivers; in fact, most of the models with this type of reverse belong to these types.
— On a keyboard switch. The control method, in many respects similar to the reverse on the start button described above, also uses a rocker switch. The key difference is that in this case the direction switch is made separately from the start button — that is, the user must first select the direction of movement, and then press "start". This option does not have any particular drawbacks, but it also does not differ in convenience, and therefore it is extremely rare.
— Gyroscopic. A rather rare and specific type of reverse, found exclusively in screwdrivers (see "Type"). In fact, there are no external switches in such a tool — instead, a built-in gyroscope is used to track body rotations. Accordingly, to select the direction of movement, you need to rather sharply turn the tool around the longitudinal axis in the appropriate direction and smoothly return it to its original position (speed can be adjusted in the same way — for example, the farther the turn, the higher the speed will be). This control method is very simple and intuitive, but it is rather complicated in technical implementation and requires increased accuracy in handling the tool. That is why gyroscopic reverse is extremely rare nowadays.
— Combined with a ratchet mechanism. Another rather rare option, found exclusively in wrenches — mostly pneumatic, less often battery-powered (see "Power"). The ratchet mechanism, we recall, is responsible for ensuring that the working part of the tool rotates in only one direction. And the reverse is controlled through a mechanical switch, which is directly connected to this mechanism and changes its settings, setting one or another direction of rotation.
The reverse allows you to switch the direction of rotation of the nozzle; see "Functions" for details. It also indicates the type of switch responsible for this function. The varieties of such switches nowadays are very diverse: slider, flag, brush on the engine, on the start button, gyroscopic, on the keyboard toggle switch, and also combined with a flow switch or ratchet mechanism. Here is a detailed description of each of these varieties:
— Crawler. Switch in the form of a slider with two opposite positions. Usually, it moves in the direction "back and forth" relative to the tool chuck — this format is considered the most practical. The sliders are quite simple and at the same time convenient and visual, especially when used in screwdrivers and wrenches: by moving forward (away from you), the direction of rotation is set to twisting, by moving backward (toward yourself), respectively, to unscrewing. However, such devices are widely used in other types of instruments (see "Device") and are generally the most popular option nowadays.
— Combined with the flow switch. The most popular type of reve...rse in pneumatic tools (see "Power Source"); not found in other models. The flow switch itself is actually a speed controller, most often in the form of a distinctive rotary knob or lever. And if this regulator is combined with a reverse, this means that it can deviate from the neutral position in two directions, and the direction of rotation will depend on which direction the flow switch is shifted.
— Flag. A switch in the form of a flag, usually installed above the start button and thrown to the right and left. One of the advantages of a checkbox is that it is right at your fingertips and can be toggled with almost no unnecessary movement (which is not always available for a slider). On the other hand, this option is mainly suitable for drills, and in screwdrivers and wrenches, the checkbox is not as intuitive as the same slider. And in general, this type of reverse for a number of reasons is much less common.
— Brush (on the engine). Reverse switch installed directly in the tool motor and based on the use of a special movable brush holder. By changing the position of the brushes in the motor with the help of such a mechanism, it is possible to change the direction of its rotation. One of the key advantages of this method is that it allows you to achieve maximum power in any direction of rotation without any special tricks. In addition, such an adjustment has a positive effect on the engine resource. On the other hand, brush switches are quite complex and expensive, and therefore are installed mainly in a powerful professional tool.
— On the start button. Reverse switch combined with start button. Such a combination button is usually made in the form of a "rocker", and the direction of rotation depends on which side of the rocker the user pressed; pressing the same button immediately starts the engine. This design allows you to easily and quickly change the direction of rotation — for this you do not need to be distracted by individual switches, just move your finger slightly and press the other half of the start button. This is especially convenient for screw and wrench drivers, as well as screwdrivers; in fact, most of the models with this type of reverse belong to these types.
— On a keyboard switch. The control method, in many respects similar to the reverse on the start button described above, also uses a rocker switch. The key difference is that in this case the direction switch is made separately from the start button — that is, the user must first select the direction of movement, and then press "start". This option does not have any particular drawbacks, but it also does not differ in convenience, and therefore it is extremely rare.
— Gyroscopic. A rather rare and specific type of reverse, found exclusively in screwdrivers (see "Type"). In fact, there are no external switches in such a tool — instead, a built-in gyroscope is used to track body rotations. Accordingly, to select the direction of movement, you need to rather sharply turn the tool around the longitudinal axis in the appropriate direction and smoothly return it to its original position (speed can be adjusted in the same way — for example, the farther the turn, the higher the speed will be). This control method is very simple and intuitive, but it is rather complicated in technical implementation and requires increased accuracy in handling the tool. That is why gyroscopic reverse is extremely rare nowadays.
— Combined with a ratchet mechanism. Another rather rare option, found exclusively in wrenches — mostly pneumatic, less often battery-powered (see "Power"). The ratchet mechanism, we recall, is responsible for ensuring that the working part of the tool rotates in only one direction. And the reverse is controlled through a mechanical switch, which is directly connected to this mechanism and changes its settings, setting one or another direction of rotation.
Air consumption
Nominal air flow rate for a tool powered by a compressor (see "Power Type"). Usually, in this case, the flow rate is implied during normal operation, under nominal pressure (see above). For normal operation of the tool, it is necessary that the compressor connected to it be able to provide no less air than indicated in the specifications — otherwise the unit will not be able to produce the required power, or even “will not start” at all.
Inlet fitting
The size of the inlet fitting is the attachment for connecting the air hose, which is equipped with a tool powered by a compressor (see "Type of power"). This parameter is traditionally indicated in fractions of an inch; the most common sizes are 1/4", 3/8" and 1/2".
Theoretically, the larger the nozzle, the higher its throughput and the better it is suitable for units with high air flow (see above). In fact, there are some exceptions to this rule (for example, rather high consumption units with a 1/4" fitting), but they are quite rare.
For proper compatibility with the compressor, it is necessary that the inlet fitting matches the air hose attachment. However, incompatibility problems can most often be solved by using adapters (although this creates some inconvenience).
Theoretically, the larger the nozzle, the higher its throughput and the better it is suitable for units with high air flow (see above). In fact, there are some exceptions to this rule (for example, rather high consumption units with a 1/4" fitting), but they are quite rare.
For proper compatibility with the compressor, it is necessary that the inlet fitting matches the air hose attachment. However, incompatibility problems can most often be solved by using adapters (although this creates some inconvenience).
Hose diameter
Nominal inner diameter of the drive hose used when the tool is powered by a compressor (see Power Type). The air required for operation enters through the drive hose; nominal usually means the smallest diameter recommended by the manufacturer in order to avoid sudden changes in the size of the air line and related troubles such as pneumatic shocks.
Theoretically, thicker hoses allow more air to be delivered and are better suited for high flow models (see above); at the same time, in fact, there is no obvious relationship between these two parameters, and the size of the drive hose is rather related to the specific technical features of each particular tool.
Theoretically, thicker hoses allow more air to be delivered and are better suited for high flow models (see above); at the same time, in fact, there is no obvious relationship between these two parameters, and the size of the drive hose is rather related to the specific technical features of each particular tool.
Cable length
The length of the cord attached to the mains powered tool (see "Power Source").
The longer the wire - the farther from the outlet you can use the tool without switching it, the more freedom the user has. On the other hand, an overly long cable creates inconvenience during storage and transportation, and even during operation it can get under your feet (or even your hands). Given this, in most cases, manufacturers equip their products with network cables from 2 to 4 m long. This gives a sufficient degree of freedom without creating inconvenience, and for situations where the length of the wire is not enough, there are extension cords. Of course, even in this range, you can choose a cable for a specific situation: for example, for a city apartment 2 - 2.5 m will be quite enough, but for a construction site it is desirable to have a longer wire.
The longer the wire - the farther from the outlet you can use the tool without switching it, the more freedom the user has. On the other hand, an overly long cable creates inconvenience during storage and transportation, and even during operation it can get under your feet (or even your hands). Given this, in most cases, manufacturers equip their products with network cables from 2 to 4 m long. This gives a sufficient degree of freedom without creating inconvenience, and for situations where the length of the wire is not enough, there are extension cords. Of course, even in this range, you can choose a cable for a specific situation: for example, for a city apartment 2 - 2.5 m will be quite enough, but for a construction site it is desirable to have a longer wire.
Weight
The total weight of the tool is usually the device itself, without attachments. For battery models (see "Power Source"), usually, the weight is indicated with a standard battery installed; for battery-powered models, the weight can be given both with and without batteries, but in this case this point is not particularly important.
Other things being equal, less weight simplifies work, increases accuracy of movement and allows you to use the tool for longer without tiring. However, note that high power and productivity inevitably increase the mass of the tool; and various tricks to reduce weight increase the price and can reduce reliability. In addition, in some cases, a massive design is more preferable. First of all, this applies to work with a large load — for example, drilling holes of large diameter, or making recesses with impact: a heavy tool is more stable, it is less prone to jerks and shifts due to uneven material, vibration of mechanisms, etc.
It is also worth noting that specific weight values are directly related to the type of tool (see "Device"). Screwdrivers are the lightest — in most of them this figure does not exceed 500 g. Screwdrivers and drill drivers are more "heavy": their average weight is 1.1 – 1.5 kg, although there are many lighter ( 0.6 – 1 kg) and heavier ( 1.6 – 2 kg or more ) models. And clas...sic drills and wrenches have the greatest weight: such a tool must be quite powerful, so for them 1.6 – 2 kg is an average, 2.1 – 2.5 kg is above average, and many units weigh more than 2, 5 kg.
Other things being equal, less weight simplifies work, increases accuracy of movement and allows you to use the tool for longer without tiring. However, note that high power and productivity inevitably increase the mass of the tool; and various tricks to reduce weight increase the price and can reduce reliability. In addition, in some cases, a massive design is more preferable. First of all, this applies to work with a large load — for example, drilling holes of large diameter, or making recesses with impact: a heavy tool is more stable, it is less prone to jerks and shifts due to uneven material, vibration of mechanisms, etc.
It is also worth noting that specific weight values are directly related to the type of tool (see "Device"). Screwdrivers are the lightest — in most of them this figure does not exceed 500 g. Screwdrivers and drill drivers are more "heavy": their average weight is 1.1 – 1.5 kg, although there are many lighter ( 0.6 – 1 kg) and heavier ( 1.6 – 2 kg or more ) models. And clas...sic drills and wrenches have the greatest weight: such a tool must be quite powerful, so for them 1.6 – 2 kg is an average, 2.1 – 2.5 kg is above average, and many units weigh more than 2, 5 kg.
Chuck type
Two points depend on the type of cartridge: the types of working tools (drills, screwdrivers, etc.) with which this or that model is compatible, and the method of installing / removing them.
— Key. As the name implies, you will need a special key to work with such a cartridge. The mount itself is usually designed for tools with round shanks (mostly drills) and includes three cams that, when clamped, converge towards the centre, clamping the tool installed in the chuck on the axis of rotation. The main disadvantage of this type of cartridge is the need to use a key: it can be lost and the mount becomes useless. In addition, installing and removing a working tool can be quite a long process. However, the key chuck is considered somewhat more reliable than the keyless chuck and more suitable for heavy work.
— Quick release. Similar to the key chuck described above, this type of chuck is designed primarily for drills with round shanks. Its main difference is the absence of a key — you can fix or remove the drill with the help of a hand, without any additional tools. Such chucks are slightly less suitable for work with high loads (for example, in hard materials and/or with large diameter drills), but otherwise they do not lose in any way with the key, and in terms of ease of use they are significantly superior.
— Under the beat. Bits are working tools us...ed in screwdrivers and screwdrivers (see "Device"). The working side of the bit can have a flat, cruciform or other shape (star, trihedron, etc.), but the shank with which it is fixed in the cartridge is standardly made hexagonal. Accordingly, the bit chuck has a recess for such a shank. Fixation can be carried out mechanically, in the form of a simple latch, or with a magnet; in both cases, the mount is secure enough for safe operation, and the tool can be removed without much effort.
— Morse taper. A cartridge for one of the varieties of the tool cone — the so-called Morse cone. As the name implies, this mount involves a conical shank and a corresponding hole for it (often with an additional groove for the protrusion on the shank — for secure fixation and prevention of rotation). This option is found mainly in drills (see "Device"). Note that the Morse cone is available in several sizes that are incompatible with each other.
— Square. The type of chuck used in impact wrenches. Unlike all other varieties, the working tool for the “square” is not installed inside the cartridge, but is put on it from the outside. Squares can have several standard sizes, but these sizes are the same for both electric and hand tools. In fact, this means that nozzles from manual wrenches can also be used in electric models if the landing size is the same (and if not the same, you can use an adapter, although this is less convenient).
— None (threaded spindle). The absence of a cartridge as such: a thread located directly on the spindle is used to fasten the working nozzles. Almost all models with this feature are powerful professional tools designed for diamond drilling (see "Intended use") — for a number of reasons, it is the threaded spindle that is considered the best way to attach nozzles for such drilling. Note that the thread on the nozzle can be both external and internal; most spindles are compatible with both varieties, but there are exceptions. So this nuance needs to be specified separately.
Note that in some models two types of cartridges can be combined — for example, for a bit and quick-clamping. Usually, for this, the kit provides two different cartridges that can be changed as needed, but there are other options — for example, a spindle into which you can insert both a bit and a drill chuck (key or keyless). Anyway, this makes the tool more versatile and allows you to work with numerous working attachments.
— Key. As the name implies, you will need a special key to work with such a cartridge. The mount itself is usually designed for tools with round shanks (mostly drills) and includes three cams that, when clamped, converge towards the centre, clamping the tool installed in the chuck on the axis of rotation. The main disadvantage of this type of cartridge is the need to use a key: it can be lost and the mount becomes useless. In addition, installing and removing a working tool can be quite a long process. However, the key chuck is considered somewhat more reliable than the keyless chuck and more suitable for heavy work.
— Quick release. Similar to the key chuck described above, this type of chuck is designed primarily for drills with round shanks. Its main difference is the absence of a key — you can fix or remove the drill with the help of a hand, without any additional tools. Such chucks are slightly less suitable for work with high loads (for example, in hard materials and/or with large diameter drills), but otherwise they do not lose in any way with the key, and in terms of ease of use they are significantly superior.
— Under the beat. Bits are working tools us...ed in screwdrivers and screwdrivers (see "Device"). The working side of the bit can have a flat, cruciform or other shape (star, trihedron, etc.), but the shank with which it is fixed in the cartridge is standardly made hexagonal. Accordingly, the bit chuck has a recess for such a shank. Fixation can be carried out mechanically, in the form of a simple latch, or with a magnet; in both cases, the mount is secure enough for safe operation, and the tool can be removed without much effort.
— Morse taper. A cartridge for one of the varieties of the tool cone — the so-called Morse cone. As the name implies, this mount involves a conical shank and a corresponding hole for it (often with an additional groove for the protrusion on the shank — for secure fixation and prevention of rotation). This option is found mainly in drills (see "Device"). Note that the Morse cone is available in several sizes that are incompatible with each other.
— Square. The type of chuck used in impact wrenches. Unlike all other varieties, the working tool for the “square” is not installed inside the cartridge, but is put on it from the outside. Squares can have several standard sizes, but these sizes are the same for both electric and hand tools. In fact, this means that nozzles from manual wrenches can also be used in electric models if the landing size is the same (and if not the same, you can use an adapter, although this is less convenient).
— None (threaded spindle). The absence of a cartridge as such: a thread located directly on the spindle is used to fasten the working nozzles. Almost all models with this feature are powerful professional tools designed for diamond drilling (see "Intended use") — for a number of reasons, it is the threaded spindle that is considered the best way to attach nozzles for such drilling. Note that the thread on the nozzle can be both external and internal; most spindles are compatible with both varieties, but there are exceptions. So this nuance needs to be specified separately.
Note that in some models two types of cartridges can be combined — for example, for a bit and quick-clamping. Usually, for this, the kit provides two different cartridges that can be changed as needed, but there are other options — for example, a spindle into which you can insert both a bit and a drill chuck (key or keyless). Anyway, this makes the tool more versatile and allows you to work with numerous working attachments.
Chuck diameter
The nominal diameter of the chuck supplied with the tool.
This size is indicated by the maximum diameter of the drill (or bit shank) that can be installed in the fixture. There are several standard sizes; the most popular nowadays are the 10 mm cartridge and the 13 mm cartridge ; drills with a 16 mm chuck are noticeably less common, as well as miniature mounts less than 10 mm(usually 8 mm or 6 mm).
The larger the drill, the more power is required for its efficient use; accordingly, larger cartridges are characteristic of heavier and more powerful tools. At the same time, it is quite possible to install a smaller cartridge on the drill, if the possibility of replacement is technically provided for at all. But the possibility of working with larger fasteners (and drills for them) should be clarified separately: not every tool has enough power for this.
This size is indicated by the maximum diameter of the drill (or bit shank) that can be installed in the fixture. There are several standard sizes; the most popular nowadays are the 10 mm cartridge and the 13 mm cartridge ; drills with a 16 mm chuck are noticeably less common, as well as miniature mounts less than 10 mm(usually 8 mm or 6 mm).
The larger the drill, the more power is required for its efficient use; accordingly, larger cartridges are characteristic of heavier and more powerful tools. At the same time, it is quite possible to install a smaller cartridge on the drill, if the possibility of replacement is technically provided for at all. But the possibility of working with larger fasteners (and drills for them) should be clarified separately: not every tool has enough power for this.
Square size
The size of the mount type "square", provided in the design of the tool.
For the mount itself, see "Chuck type", here we just recall that squares are mainly used in wrenches for installing socket heads. At the same time, for larger nozzles, usually, larger mounts are also used. And the sizes of squares are traditionally indicated by fractional parts of an inch. The most popular option is the 1/2" square, it is the most versatile. Both larger sizes ( 3/4" square and 1" square) and smaller ones ( 3/8" square and 1/4" square) are somewhat less common. ).
Note that there are adapters that allow you to install nozzles of a “non-native” size on a square. However, the possibility of using larger nozzles than regular ones should be clarified separately: the tool may not have enough power for this. In addition, single wrench models are available that initially provide a replacement square and are equipped with interchangeable fasteners — usually 1/4" and 3/8", but other options are also possible.
For the mount itself, see "Chuck type", here we just recall that squares are mainly used in wrenches for installing socket heads. At the same time, for larger nozzles, usually, larger mounts are also used. And the sizes of squares are traditionally indicated by fractional parts of an inch. The most popular option is the 1/2" square, it is the most versatile. Both larger sizes ( 3/4" square and 1" square) and smaller ones ( 3/8" square and 1/4" square) are somewhat less common. ).
Note that there are adapters that allow you to install nozzles of a “non-native” size on a square. However, the possibility of using larger nozzles than regular ones should be clarified separately: the tool may not have enough power for this. In addition, single wrench models are available that initially provide a replacement square and are equipped with interchangeable fasteners — usually 1/4" and 3/8", but other options are also possible.
Quick chuck change
The ability to quickly remove the cartridge and replace it with another, and, usually, by hand, without the use of additional tools. A quick change of cartridge is found mainly in drill drivers (see "Device"): in different modes, such devices require different types of cartridges (one for a drill, the other for a bit), and the ability to quickly change one type to another in some situations is extremely useful .
Wood drilling max. ⌀
The largest diameter of holes that the tool can make when drilling with a conventional drill in wood.
The larger the hole diameter, the higher the resistance of the material, the more power the tool must provide and the higher the load on it. Therefore, the maximum allowable drilling diameter must not be exceeded, even if the chuck allows you to install a thicker drill bit — this can lead to tool breakage and even injury to others.
It is worth noting that some types of wood can have a fairly high density, and for them the actual allowable drill diameter will be, accordingly, less than the claimed one. However, this is true mainly for exotic breeds, which are extremely rare in our area.
The larger the hole diameter, the higher the resistance of the material, the more power the tool must provide and the higher the load on it. Therefore, the maximum allowable drilling diameter must not be exceeded, even if the chuck allows you to install a thicker drill bit — this can lead to tool breakage and even injury to others.
It is worth noting that some types of wood can have a fairly high density, and for them the actual allowable drill diameter will be, accordingly, less than the claimed one. However, this is true mainly for exotic breeds, which are extremely rare in our area.
Metal drilling max. ⌀
The largest diameter of holes that the tool is capable of making when drilling with a conventional drill in metal.
The larger the hole diameter, the higher the resistance of the material, the more power the tool must provide and the higher the load on it. Therefore, the maximum allowable drilling diameter must not be exceeded, even if the chuck allows you to install a thicker drill bit — this can lead to tool breakage and even injury to others.
Also note that the drilling diameter for metal is usually indicated based on medium hard steel and other similar materials. For metals and alloys that have a significantly higher hardness and density, the allowable drill thickness will be less; however, such situations occur infrequently, and if you wish, you can find out about the features of working with various alloys x in special sources.
The larger the hole diameter, the higher the resistance of the material, the more power the tool must provide and the higher the load on it. Therefore, the maximum allowable drilling diameter must not be exceeded, even if the chuck allows you to install a thicker drill bit — this can lead to tool breakage and even injury to others.
Also note that the drilling diameter for metal is usually indicated based on medium hard steel and other similar materials. For metals and alloys that have a significantly higher hardness and density, the allowable drill thickness will be less; however, such situations occur infrequently, and if you wish, you can find out about the features of working with various alloys x in special sources.
Concrete drilling max. ⌀
The largest diameter of the holes that the tool is capable of making when drilling with a conventional drill in concrete. It is worth considering that in this case we are not talking about reinforced concrete — this material requires special methods of influence (ideally, the use of diamond crowns).
The larger the hole diameter, the higher the resistance of the material, the more power the tool must provide and the higher the load on it. Therefore, the maximum allowable drilling diameter must not be exceeded, even if the chuck allows you to install a thicker drill bit — this can lead to tool breakage and even injury to others.
The larger the hole diameter, the higher the resistance of the material, the more power the tool must provide and the higher the load on it. Therefore, the maximum allowable drilling diameter must not be exceeded, even if the chuck allows you to install a thicker drill bit — this can lead to tool breakage and even injury to others.
Masonry drilling max. ⌀
The largest diameter of holes that the tool can make when drilling with a conventional drill in masonry.
The larger the hole diameter, the higher the resistance of the material, the more power the tool must provide and the higher the load on it. Therefore, the maximum allowable drilling diameter must not be exceeded, even if the chuck allows you to install a thicker drill bit - this can lead to tool breakage and even injury to others.
It should be borne in mind that for denser masonry, the actual allowable drill diameter may be less than the declared one. However, this is often indicated in the characteristics of the corresponding tool in a separate line.
The larger the hole diameter, the higher the resistance of the material, the more power the tool must provide and the higher the load on it. Therefore, the maximum allowable drilling diameter must not be exceeded, even if the chuck allows you to install a thicker drill bit - this can lead to tool breakage and even injury to others.
It should be borne in mind that for denser masonry, the actual allowable drill diameter may be less than the declared one. However, this is often indicated in the characteristics of the corresponding tool in a separate line.
Max. hole saw ⌀
The largest hole diameter the tool can make when using a hole saw. Usually, speaking of crowns, they mean drilling concrete; when it comes to other materials, these details are usually specified separately.
This parameter is most relevant for tools for diamond drilling (see "Intended use"), however, core bits can also be used in more traditional drills. Recall that such a nozzle has the form of a hollow cylinder and cuts out not a finished hole, but only its circumference — which means that it experiences much less resistance than a drill. Therefore, a much larger hole can be made in this way: for example, a drill that cannot use drills larger than 20 mm with concrete may well allow the use of crowns of 100 or even 150 mm.
Returning to the maximum diameter, we recall that in no case should it be exceeded — this can lead to tool breakage and injury to people.
This parameter is most relevant for tools for diamond drilling (see "Intended use"), however, core bits can also be used in more traditional drills. Recall that such a nozzle has the form of a hollow cylinder and cuts out not a finished hole, but only its circumference — which means that it experiences much less resistance than a drill. Therefore, a much larger hole can be made in this way: for example, a drill that cannot use drills larger than 20 mm with concrete may well allow the use of crowns of 100 or even 150 mm.
Returning to the maximum diameter, we recall that in no case should it be exceeded — this can lead to tool breakage and injury to people.
Features
— Impact mode. Ability to work in the so-called shock mode. Usually, this mode is turned on and off at the request of the user, and its meaning and features may be different, depending on the type of instrument (see "Device"). So, in drills, strikes are carried out along the axis of the drill, and their frequency is usually several thousand per minute — this has a positive effect on productivity and allows you to more effectively cope with hard, dense materials (although such a drill can not be replaced anyway). In turn, in screwdrivers and wrenches, it would be more correct to call the impact mode pulsed: in this format of operation, the tool nozzle does not rotate uniformly, but in separate jerks, usually at a frequency of about 3K per minute. It also improves work efficiency, which is especially useful when driving self-tapping screws into dense material and unscrewing old, “stuck” fasteners.
— Engine brake. A device that additionally slows down the engine when the tool is turned off. The engine itself (and, accordingly, the working nozzle) after turning off can rotate for quite a long time by inertia; the brake stops this rotation almost immediately, so you do not have to keep the tool on weight for too long.
— Power button lock. A function that allows you to lock the power button in the pressed position. Usually, it looks like an additional button insta...lled either on the start key itself or not far from it. This function is very convenient in situations where the tool has to be used for a long time without interruption — for example, when drilling several dozen holes at once: it is easier to fix the start button in the on position than to keep it pressed all the time, additionally straining the finger on the working hand. And the lock is turned off, usually, in the simplest way — for example, by briefly pressing the same start button.
— Speed controller. Possibility to additionally limit the revolutions of the tool. By itself, smooth adjustment is available in almost all modern models: the harder you press the start button, the higher the speed. This allows you to directly "on the go" adjust the mode of operation of the tool to the specifics of the situation. And this regulator allows you to set the maximum speed of rotation, so that even when you press the button “to the stop”, the speed of the working nozzle does not exceed the specified value. This function is indispensable for some jobs that require precision — in particular, when processing delicate materials, for which too high a speed is fraught with damage.
Separately, we emphasize that the presence of a speed controller has nothing to do with the number of speeds (see above). For example, a tool may well have several speed modes, in each of which the speed can be further limited using a regulator.
— Maintain momentum. A feature that allows you to maintain a constant speed of rotation of the nozzle, regardless of the load on it. Without special adjustment, at a constant engine power, the rotational speed inevitably drops with increasing load and increases with a decrease. And the revs control system monitors the resistance on the nozzle and, if necessary, changes the power in such a way that the rotation speed remains constant. This has a positive effect both on the quality of work and on the service life of the nozzles and the entire tool.
— Electronic engine protection. A system that protects the engine from critical overloads — for example, in the event of a jammed drill — and overheating. If the motor load or motor temperature is exceeded, the power to the instrument is automatically turned off to avoid damage to the instrument.
— Brushless motor. The presence of a brushless (brushless) motor in an electric tool. Such motors are noticeably superior to traditional collector motors in terms of efficiency, which can significantly reduce energy consumption without sacrificing power; this is especially important for cordless tools (see "Power Source"), where this feature is predominantly found. In addition, brushless motors are quieter and produce virtually no sparks during operation, making them perfect for working in high fire hazard environments. Their main disadvantages are traditional — the complexity of the design and high price.
— Safety clutch. A device that protects the engine from damage during a sharp increase in load (for example, due to jamming of the drill). In such cases, the safety clutch disconnects the motor shaft from the tool chuck, avoiding overloads. Note that such devices can be both reusable and disposable — the latter are destroyed when triggered, and to continue working, you will need to install a new clutch.
— Backlight. The built-in lamp for illumination of a place of work. This feature can be useful both in the evening/night time, and in hard-to-reach places where there is little penetration of outdoor lighting, as well as in situations where this lighting is too dim. Note that in addition to built-in light sources, modern tools can also be equipped with separate flashlights; for more details about them, see "Complete set".
— Display. Own display, which can display various information about the operation and status of the device — for example, the torque or rotation speed set in the settings, and in battery models, there is also a battery charge indicator. Such a screen provides additional convenience and visibility, however, in general, this is a rather specific function that is extremely rare in modern power tools — for example, a speed or torque indicator can be provided directly on the regulator, and a conventional LED can be provided as a charge indicator, giving signals by blinking or colour change.
— Synchronization with a smartphone. The ability to connect the instrument to a smartphone or other gadget (such as a tablet) via Wi-Fi or Bluetooth. Such a connection is usually used to adjust operating parameters such as speed or torque; doing this through a mobile application is often more convenient than through the controls on the instrument itself. And some models with this function also allow you to set password access: the tool simply will not respond to the start button until the correct password is entered on the control gadget.
— Built-in bubble level. Built-in device to control the angle at which the tool is located to the horizon. As in ordinary levels, the role of the scale in such devices is played by a sealed flask with marks applied to it, containing a brightly coloured liquid and an air bubble. By the position of this bubble relative to the marks, the position of the entire tool is determined — namely, its correspondence to the vertical, horizontal, or pre-set tilt angle (the latter option, however, is almost never found in the built-in levels). At the same time, purely hand tools usually provide a single-axis level that reacts only to deviation from the horizontal forward or backward, and models with the ability to mount on a rack (see below) can also have a circular level that controls compliance with the vertical and determines deviations from it in any direction.
— Revolving mechanism for bits. A mechanism for storing and quickly changing bits used in tools for the corresponding purpose — mainly screwdrivers, but also some screwdrivers (see "Device"). In accordance with the name, the main part of the mechanism is a drum like a revolver, in the compartments of which the bits are stored. The mechanism is located behind the cartridge, and the choice of bits usually occurs as follows: you need to pull back a special casing or handle (if at that moment there was another bit in the cartridge, it will return to the drum), by turning the drum, select the compartment with the desired nozzle, and then move the casing / handle to its original position by pushing the nozzle out of the drum into the chuck. This feature significantly speeds up and simplifies the replacement of nozzles, and also reduces the risk of losing them. On the other hand, the revolving mechanism significantly affects the price and weight of the tool, and its capacity is usually limited to 6 – 8 nozzles. Thus, such a tool is usually also equipped with an adapter for installing bits in the traditional way, from the outside of the cartridge.
— Water cooling(coolant). The tool has a coolant — a liquid cooling system (most often plain water) supplied to the working nozzle using a built-in pump. Such a system performs several functions at once. Firstly, it actually cools the nozzle, preventing damage due to overheating. Secondly, the liquid somewhat reduces friction at the point of contact, further reducing the load on the nozzle and increasing its durability. Thirdly, water absorbs dust generated during drilling, this dust does not fly into the air and does not enter the lungs of people around; and cleaning up after work is much easier. On the other hand, water cooling systems are quite expensive and bulky, and with relatively simple work and low loads, it is quite possible to do without coolant.
— Soft start. A function that provides a smooth spin-up of the tool motor, with relatively little acceleration. This is achieved by limiting the starting current. Without such a limit, the current drawn by the motor at the time of starting can be quite high, causing the motor to start very abruptly, which increases the risk of letting go of the tool. In addition, current surges can lead to overloads in the network used for power. Soft start allows you to eliminate these phenomena to some extent. Note that it is used only in mains-powered models — the motors in cordless tools are not so powerful that they have the actual “troubles” described for them.
— Engine brake. A device that additionally slows down the engine when the tool is turned off. The engine itself (and, accordingly, the working nozzle) after turning off can rotate for quite a long time by inertia; the brake stops this rotation almost immediately, so you do not have to keep the tool on weight for too long.
— Power button lock. A function that allows you to lock the power button in the pressed position. Usually, it looks like an additional button insta...lled either on the start key itself or not far from it. This function is very convenient in situations where the tool has to be used for a long time without interruption — for example, when drilling several dozen holes at once: it is easier to fix the start button in the on position than to keep it pressed all the time, additionally straining the finger on the working hand. And the lock is turned off, usually, in the simplest way — for example, by briefly pressing the same start button.
— Speed controller. Possibility to additionally limit the revolutions of the tool. By itself, smooth adjustment is available in almost all modern models: the harder you press the start button, the higher the speed. This allows you to directly "on the go" adjust the mode of operation of the tool to the specifics of the situation. And this regulator allows you to set the maximum speed of rotation, so that even when you press the button “to the stop”, the speed of the working nozzle does not exceed the specified value. This function is indispensable for some jobs that require precision — in particular, when processing delicate materials, for which too high a speed is fraught with damage.
Separately, we emphasize that the presence of a speed controller has nothing to do with the number of speeds (see above). For example, a tool may well have several speed modes, in each of which the speed can be further limited using a regulator.
— Maintain momentum. A feature that allows you to maintain a constant speed of rotation of the nozzle, regardless of the load on it. Without special adjustment, at a constant engine power, the rotational speed inevitably drops with increasing load and increases with a decrease. And the revs control system monitors the resistance on the nozzle and, if necessary, changes the power in such a way that the rotation speed remains constant. This has a positive effect both on the quality of work and on the service life of the nozzles and the entire tool.
— Electronic engine protection. A system that protects the engine from critical overloads — for example, in the event of a jammed drill — and overheating. If the motor load or motor temperature is exceeded, the power to the instrument is automatically turned off to avoid damage to the instrument.
— Brushless motor. The presence of a brushless (brushless) motor in an electric tool. Such motors are noticeably superior to traditional collector motors in terms of efficiency, which can significantly reduce energy consumption without sacrificing power; this is especially important for cordless tools (see "Power Source"), where this feature is predominantly found. In addition, brushless motors are quieter and produce virtually no sparks during operation, making them perfect for working in high fire hazard environments. Their main disadvantages are traditional — the complexity of the design and high price.
— Safety clutch. A device that protects the engine from damage during a sharp increase in load (for example, due to jamming of the drill). In such cases, the safety clutch disconnects the motor shaft from the tool chuck, avoiding overloads. Note that such devices can be both reusable and disposable — the latter are destroyed when triggered, and to continue working, you will need to install a new clutch.
— Backlight. The built-in lamp for illumination of a place of work. This feature can be useful both in the evening/night time, and in hard-to-reach places where there is little penetration of outdoor lighting, as well as in situations where this lighting is too dim. Note that in addition to built-in light sources, modern tools can also be equipped with separate flashlights; for more details about them, see "Complete set".
— Display. Own display, which can display various information about the operation and status of the device — for example, the torque or rotation speed set in the settings, and in battery models, there is also a battery charge indicator. Such a screen provides additional convenience and visibility, however, in general, this is a rather specific function that is extremely rare in modern power tools — for example, a speed or torque indicator can be provided directly on the regulator, and a conventional LED can be provided as a charge indicator, giving signals by blinking or colour change.
— Synchronization with a smartphone. The ability to connect the instrument to a smartphone or other gadget (such as a tablet) via Wi-Fi or Bluetooth. Such a connection is usually used to adjust operating parameters such as speed or torque; doing this through a mobile application is often more convenient than through the controls on the instrument itself. And some models with this function also allow you to set password access: the tool simply will not respond to the start button until the correct password is entered on the control gadget.
— Built-in bubble level. Built-in device to control the angle at which the tool is located to the horizon. As in ordinary levels, the role of the scale in such devices is played by a sealed flask with marks applied to it, containing a brightly coloured liquid and an air bubble. By the position of this bubble relative to the marks, the position of the entire tool is determined — namely, its correspondence to the vertical, horizontal, or pre-set tilt angle (the latter option, however, is almost never found in the built-in levels). At the same time, purely hand tools usually provide a single-axis level that reacts only to deviation from the horizontal forward or backward, and models with the ability to mount on a rack (see below) can also have a circular level that controls compliance with the vertical and determines deviations from it in any direction.
— Revolving mechanism for bits. A mechanism for storing and quickly changing bits used in tools for the corresponding purpose — mainly screwdrivers, but also some screwdrivers (see "Device"). In accordance with the name, the main part of the mechanism is a drum like a revolver, in the compartments of which the bits are stored. The mechanism is located behind the cartridge, and the choice of bits usually occurs as follows: you need to pull back a special casing or handle (if at that moment there was another bit in the cartridge, it will return to the drum), by turning the drum, select the compartment with the desired nozzle, and then move the casing / handle to its original position by pushing the nozzle out of the drum into the chuck. This feature significantly speeds up and simplifies the replacement of nozzles, and also reduces the risk of losing them. On the other hand, the revolving mechanism significantly affects the price and weight of the tool, and its capacity is usually limited to 6 – 8 nozzles. Thus, such a tool is usually also equipped with an adapter for installing bits in the traditional way, from the outside of the cartridge.
— Water cooling(coolant). The tool has a coolant — a liquid cooling system (most often plain water) supplied to the working nozzle using a built-in pump. Such a system performs several functions at once. Firstly, it actually cools the nozzle, preventing damage due to overheating. Secondly, the liquid somewhat reduces friction at the point of contact, further reducing the load on the nozzle and increasing its durability. Thirdly, water absorbs dust generated during drilling, this dust does not fly into the air and does not enter the lungs of people around; and cleaning up after work is much easier. On the other hand, water cooling systems are quite expensive and bulky, and with relatively simple work and low loads, it is quite possible to do without coolant.
— Soft start. A function that provides a smooth spin-up of the tool motor, with relatively little acceleration. This is achieved by limiting the starting current. Without such a limit, the current drawn by the motor at the time of starting can be quite high, causing the motor to start very abruptly, which increases the risk of letting go of the tool. In addition, current surges can lead to overloads in the network used for power. Soft start allows you to eliminate these phenomena to some extent. Note that it is used only in mains-powered models — the motors in cordless tools are not so powerful that they have the actual “troubles” described for them.
In box
- Corner nozzle. A nozzle that allows you to rotate the axis of rotation of the cartridge by 90 ° relative to its original position. Such a device is indispensable for making holes, as well as twisting and unscrewing fasteners in some hard-to-reach places (for example, in narrow grooves or a profile).
- Eccentric nozzle. Replaceable nozzle designed to shift the axis of rotation of the cartridge slightly away from its original position. In this case, the direction of the axis remains the same. Like the corner nozzle, such a device is intended mainly for working in certain hard-to-reach places (in particular, near walls and edges of workpieces).
- Additional handle. A modern tool, even a relatively low-power one, can be quite massive, and for maximum accuracy and reliability it may be necessary to hold it with two hands at once. Using an additional handle for this is more convenient and safer than looking for a place to grip on the body. The handles themselves are usually mounted near the cartridge perpendicular to the axis of rotation and may have different design features.
- Depth stop. A device that allows you to limit the depth of drilling. The most popular version of such a limiter is a rod in a special mount, installed parallel to the drill. Before starting work, this rod is shifted so that when the desired depth is reached, its end rests on the surface of the material,...preventing the drill from moving further.
- Store nozzle. It looks like a kind of store or disk, into which a tape with self-tapping screws is “charged”; and a special block is installed in front of the cartridge, designed to supply self-tapping screws. This design allows you to tighten the screws as quickly as possible and without unnecessary movements: just load the tape from the magazine into the feed unit, start the engine and alternately press the working part of the tool to the desired points on the material.
- Lantern. A classic flashlight for illumination in low light conditions, in contrast to the built-in illumination system, is a separate device. Such a separate device is not very convenient to hold in your hand during work - in such cases you can’t take the tool with both hands, and this creates problems in some situations. On the other hand, often the situation allows you to put or hang a lantern without taking up your hands; and sometimes in this way you can even organize the lighting more successfully than using the built-in backlight. In addition, the flashlight can be used independently.
- Case (bag) included. The presence of a case or bag in the delivery set of the drill. Cases are usually called hard suitcases; bags, unlike cases, are soft, which allows them to be packed more tightly together with other things, but reduces the degree of protection. In any case, this feature makes the tool more convenient to store and carry: the complete bag or case is optimally suited for this model, in addition, they can hold drills, spare batteries and other additional accessories.
- Rack. Mostly professional drills for diamond drilling are completed with racks(see "Purpose"). This design is a stand (base) with a guide rail fixed on it, along which the tool can move using a special mechanism. According to the fastening of the rail, the racks are divided into two types:
- A set of drills. The presence of drills in the kit eliminates the need to purchase them separately and allows you to use a drill (or other tool with drill functions) right out of the box. True, the specific assortment of drills can be different - besides, it is often an entry-level set of 5 to 7 devices for the simplest tasks like drilling wood. However, even such a set will be useful if the tool is purchased for domestic use or simple work that does not require specialized nozzles. We also note that such equipment is especially convenient when buying a “first tool for a beginner”, when there are no drills on the farm yet and one way or another you will have to buy them.
- A set of bits. Bits, we recall, are nozzles in the form of screwdriver heads, which are also used in screwdrivers. As in the case of drills, the presence of such nozzles in the kit eliminates the need to purchase them separately and makes it possible to use the tool immediately after purchase. The specific set of bits is worth specifying further, but most often it includes at least flat and cross bits in a fairly large variety of sizes. And in general, such sets are quite extensive - even in relatively inexpensive tools, the number of complete bits can be measured in tens.
- Equipment. The term "equipment" means at least several types of working nozzles, and sometimes additional accessories. For example, if such equipment is indicated for a drill-driver, then this model is almost guaranteed to be equipped with both drills and bits (and possibly more specific accessories). A specific set of equipment should be specified separately.
- Extension. The purpose of such an accessory is clear from the name: it allows you to increase the working length of the tool. In other words, when you install an extension bat or other equipment, it is further from the body; the extension itself is made quite thin. This accessory is used mainly in models with the functions of a screwdriver or wrench: it allows you to reach deep-seated fasteners that are inaccessible in the usual configuration. And in many models, the extension cord is also made flexible, which further expands its capabilities.
- Magnetizer. Device for magnetizing bolts, screws and other similar fasteners. Found in individual screwdrivers; the working tooling of such tools is also made of magnetic material, due to which the magnetized fastener effectively “sticks” to the tooling and does not need to be supported separately.
- Case insert. Interchangeable insert (or several inserts) to adjust the complete case to the specific situation. For example, a regular insert can only have space for a tool and a charger, and a replacement one can also accommodate a second spare battery. Specific features should be specified separately.
- Charger(charger). A device for charging the batteries used in the tool with the appropriate power supply. For models supplied with such a device, the charger model may be additionally specified in the characteristics. This information can be useful not only for finding a spare or replacement charger, but also in case the household has other cordless tools and / or batteries for them. The fact is that many manufacturers nowadays use universal batteries that are compatible with a whole set of tools from the same brand; so, for example, a complete charger for a drill may be quite suitable for a cordless grinder from the same manufacturer.
On the other hand, a lot of modern cordless tools come without a charger at all. This option will be optimal, first of all, if a compatible memory is already available, and there is simply no need to overpay for a second device. In addition, the lack of a charger will be appreciated by those who want to choose this accessory separately, without relying on the manufacturer's decision.
Note that the above list is not complete - modern tools can be supplied with other additional items, including very unexpected and original ones - like a fitness tracker or even a radio-controlled car.
- Eccentric nozzle. Replaceable nozzle designed to shift the axis of rotation of the cartridge slightly away from its original position. In this case, the direction of the axis remains the same. Like the corner nozzle, such a device is intended mainly for working in certain hard-to-reach places (in particular, near walls and edges of workpieces).
- Additional handle. A modern tool, even a relatively low-power one, can be quite massive, and for maximum accuracy and reliability it may be necessary to hold it with two hands at once. Using an additional handle for this is more convenient and safer than looking for a place to grip on the body. The handles themselves are usually mounted near the cartridge perpendicular to the axis of rotation and may have different design features.
- Depth stop. A device that allows you to limit the depth of drilling. The most popular version of such a limiter is a rod in a special mount, installed parallel to the drill. Before starting work, this rod is shifted so that when the desired depth is reached, its end rests on the surface of the material,...preventing the drill from moving further.
- Store nozzle. It looks like a kind of store or disk, into which a tape with self-tapping screws is “charged”; and a special block is installed in front of the cartridge, designed to supply self-tapping screws. This design allows you to tighten the screws as quickly as possible and without unnecessary movements: just load the tape from the magazine into the feed unit, start the engine and alternately press the working part of the tool to the desired points on the material.
- Lantern. A classic flashlight for illumination in low light conditions, in contrast to the built-in illumination system, is a separate device. Such a separate device is not very convenient to hold in your hand during work - in such cases you can’t take the tool with both hands, and this creates problems in some situations. On the other hand, often the situation allows you to put or hang a lantern without taking up your hands; and sometimes in this way you can even organize the lighting more successfully than using the built-in backlight. In addition, the flashlight can be used independently.
- Case (bag) included. The presence of a case or bag in the delivery set of the drill. Cases are usually called hard suitcases; bags, unlike cases, are soft, which allows them to be packed more tightly together with other things, but reduces the degree of protection. In any case, this feature makes the tool more convenient to store and carry: the complete bag or case is optimally suited for this model, in addition, they can hold drills, spare batteries and other additional accessories.
- Rack. Mostly professional drills for diamond drilling are completed with racks(see "Purpose"). This design is a stand (base) with a guide rail fixed on it, along which the tool can move using a special mechanism. According to the fastening of the rail, the racks are divided into two types:
- Non-inclined stand. A structure with a rigidly fixed rail, which is usually located vertically, perpendicular to the base; accordingly, the axis of rotation of the installed tool also remains always vertical. Such racks have more limited capabilities than inclined ones. On the other hand, they are simpler, cheaper and more reliable (there is no movable mount in the design that can become loose); and for most work, the vertical position of the tool is fine.
- Tilt stand. Stands in which the rail is fixed on a swivel mount and can deviate from the vertical at a certain angle. Accordingly, such a device allows you to direct the crown not only vertically, but also at an angle; this can be important for some non-standard tasks. On the other hand, a movable structure is more complex, expensive and less durable than a fixed one; therefore, it is worth paying attention to this option if the possibility of inclined drilling is fundamental for you.
- A set of drills. The presence of drills in the kit eliminates the need to purchase them separately and allows you to use a drill (or other tool with drill functions) right out of the box. True, the specific assortment of drills can be different - besides, it is often an entry-level set of 5 to 7 devices for the simplest tasks like drilling wood. However, even such a set will be useful if the tool is purchased for domestic use or simple work that does not require specialized nozzles. We also note that such equipment is especially convenient when buying a “first tool for a beginner”, when there are no drills on the farm yet and one way or another you will have to buy them.
- A set of bits. Bits, we recall, are nozzles in the form of screwdriver heads, which are also used in screwdrivers. As in the case of drills, the presence of such nozzles in the kit eliminates the need to purchase them separately and makes it possible to use the tool immediately after purchase. The specific set of bits is worth specifying further, but most often it includes at least flat and cross bits in a fairly large variety of sizes. And in general, such sets are quite extensive - even in relatively inexpensive tools, the number of complete bits can be measured in tens.
- Equipment. The term "equipment" means at least several types of working nozzles, and sometimes additional accessories. For example, if such equipment is indicated for a drill-driver, then this model is almost guaranteed to be equipped with both drills and bits (and possibly more specific accessories). A specific set of equipment should be specified separately.
- Extension. The purpose of such an accessory is clear from the name: it allows you to increase the working length of the tool. In other words, when you install an extension bat or other equipment, it is further from the body; the extension itself is made quite thin. This accessory is used mainly in models with the functions of a screwdriver or wrench: it allows you to reach deep-seated fasteners that are inaccessible in the usual configuration. And in many models, the extension cord is also made flexible, which further expands its capabilities.
- Magnetizer. Device for magnetizing bolts, screws and other similar fasteners. Found in individual screwdrivers; the working tooling of such tools is also made of magnetic material, due to which the magnetized fastener effectively “sticks” to the tooling and does not need to be supported separately.
- Case insert. Interchangeable insert (or several inserts) to adjust the complete case to the specific situation. For example, a regular insert can only have space for a tool and a charger, and a replacement one can also accommodate a second spare battery. Specific features should be specified separately.
- Charger(charger). A device for charging the batteries used in the tool with the appropriate power supply. For models supplied with such a device, the charger model may be additionally specified in the characteristics. This information can be useful not only for finding a spare or replacement charger, but also in case the household has other cordless tools and / or batteries for them. The fact is that many manufacturers nowadays use universal batteries that are compatible with a whole set of tools from the same brand; so, for example, a complete charger for a drill may be quite suitable for a cordless grinder from the same manufacturer.
On the other hand, a lot of modern cordless tools come without a charger at all. This option will be optimal, first of all, if a compatible memory is already available, and there is simply no need to overpay for a second device. In addition, the lack of a charger will be appreciated by those who want to choose this accessory separately, without relying on the manufacturer's decision.
Note that the above list is not complete - modern tools can be supplied with other additional items, including very unexpected and original ones - like a fitness tracker or even a radio-controlled car.
Power source
- Mains. Power supply from household network 230 V. Such a tool can have almost any power, while it costs less and weighs less than a similar cordless one. On the other hand, freedom of movement when working with such drills is limited by the presence of sockets and the length of the power cord and existing extension cords, and the cord itself can create inconvenience.
— Mains (110 V). Tools powered in the American and Japanese style - from electrical networks with a voltage of 110 V. Drills and screwdrivers with this operating voltage are produced for the market of North and Central America, the Land of the Rising Sun, and Saudi Arabia. 110V electrical systems are also found in the UK. To avoid failure of the instrument when connected to standard 230 V household networks, you will need an additional connecting link in the form of a step-down transformer or a special 110 V converter.
— Battery. The presence of a battery allows you to avoid many problems - when moving to another part of the room, you no longer have to switch the wire. In addition, you can use the tool in places where there is no power supply at all - for example, at the remote end of a summer cottage. At the same time, with equal power, such models are much heavier and more expensive than mains-powered tools, and the battery life is limited - when the charge is depleted, the battery will...have to be recharged or replaced with a fresh one. Luckily, many drills come with two or more batteries included; For more details, see "Advanced".
— Pneumatic (compressor). Models driven by compressed air from a compressor. Such power supply is fundamentally different from electric power supply, as a result of which it has a number of advantages. Thus, with similar performance characteristics, pneumatic tools are simpler and more compact, which significantly increases both the overall ease of use and the ability to access hard-to-reach places. They can be used where power tools are unacceptable due to safety requirements - in places with high humidity or an abundance of metal dust, etc.; for example, one of the traditional areas of use of pneumatic tools is service stations. In addition, such models are better suited for long-term work. Among the disadvantages of this option, it is worth noting the difficulty in connecting and the high cost of operation: a compressor is required for operation, and the efficiency of the entire system is quite low, which increases costs.
— Electrical network (12 V). Power supply from the on-board electrical network of a passenger car or other similar vehicle - the standard voltage of such networks is exactly 12 V. This option is found exclusively in tools of the corresponding specialization (see “Purpose”); Such a tool is connected to a cigarette lighter socket or a car socket of a similar format, and its power is usually very low - on-board car networks, in principle, are not designed for high loads.
— Battery/mains (12 V). Tools that can operate both from their own battery and from a 12 V car electrical system (in other words, from the cigarette lighter socket). The features of each type of food are described in detail above. Here we note that despite the presence of a battery and the possibility of autonomous operation, tools with this power supply format are still most often classified as automotive (see “Purpose”) - primarily because it is usually supposed to charge a dead battery from the cigarette lighter.
— AA batteries. Powered by replaceable elements of size AA (“finger”) or AAA (“little finger”). The specific type and number of such elements depend on the “weight category” of the tool, but in any case they do not allow achieving high power, and therefore are used mainly in compact and low-power devices - mainly screwdrivers (see “Type”), including those used for precision work (see “Purpose”). This type of power supply is well suited for such models due to the relatively light weight and size of the batteries. In addition, when the charge is depleted, the battery can be quickly replaced without wasting time on charging (unlike built-in batteries). True, the elements themselves are usually not included in the delivery package; they need to be purchased separately - on the other hand, you can choose a specific brand of batteries at your discretion. In addition, let us remind you that in addition to disposable batteries, rechargeable batteries are also produced in this form factor - they are noticeably more expensive, but more convenient for frequent and long-term use; in turn, disposable elements are best suited for rare, occasional use.
— Mains (110 V). Tools powered in the American and Japanese style - from electrical networks with a voltage of 110 V. Drills and screwdrivers with this operating voltage are produced for the market of North and Central America, the Land of the Rising Sun, and Saudi Arabia. 110V electrical systems are also found in the UK. To avoid failure of the instrument when connected to standard 230 V household networks, you will need an additional connecting link in the form of a step-down transformer or a special 110 V converter.
— Battery. The presence of a battery allows you to avoid many problems - when moving to another part of the room, you no longer have to switch the wire. In addition, you can use the tool in places where there is no power supply at all - for example, at the remote end of a summer cottage. At the same time, with equal power, such models are much heavier and more expensive than mains-powered tools, and the battery life is limited - when the charge is depleted, the battery will...have to be recharged or replaced with a fresh one. Luckily, many drills come with two or more batteries included; For more details, see "Advanced".
— Pneumatic (compressor). Models driven by compressed air from a compressor. Such power supply is fundamentally different from electric power supply, as a result of which it has a number of advantages. Thus, with similar performance characteristics, pneumatic tools are simpler and more compact, which significantly increases both the overall ease of use and the ability to access hard-to-reach places. They can be used where power tools are unacceptable due to safety requirements - in places with high humidity or an abundance of metal dust, etc.; for example, one of the traditional areas of use of pneumatic tools is service stations. In addition, such models are better suited for long-term work. Among the disadvantages of this option, it is worth noting the difficulty in connecting and the high cost of operation: a compressor is required for operation, and the efficiency of the entire system is quite low, which increases costs.
— Electrical network (12 V). Power supply from the on-board electrical network of a passenger car or other similar vehicle - the standard voltage of such networks is exactly 12 V. This option is found exclusively in tools of the corresponding specialization (see “Purpose”); Such a tool is connected to a cigarette lighter socket or a car socket of a similar format, and its power is usually very low - on-board car networks, in principle, are not designed for high loads.
— Battery/mains (12 V). Tools that can operate both from their own battery and from a 12 V car electrical system (in other words, from the cigarette lighter socket). The features of each type of food are described in detail above. Here we note that despite the presence of a battery and the possibility of autonomous operation, tools with this power supply format are still most often classified as automotive (see “Purpose”) - primarily because it is usually supposed to charge a dead battery from the cigarette lighter.
— AA batteries. Powered by replaceable elements of size AA (“finger”) or AAA (“little finger”). The specific type and number of such elements depend on the “weight category” of the tool, but in any case they do not allow achieving high power, and therefore are used mainly in compact and low-power devices - mainly screwdrivers (see “Type”), including those used for precision work (see “Purpose”). This type of power supply is well suited for such models due to the relatively light weight and size of the batteries. In addition, when the charge is depleted, the battery can be quickly replaced without wasting time on charging (unlike built-in batteries). True, the elements themselves are usually not included in the delivery package; they need to be purchased separately - on the other hand, you can choose a specific brand of batteries at your discretion. In addition, let us remind you that in addition to disposable batteries, rechargeable batteries are also produced in this form factor - they are noticeably more expensive, but more convenient for frequent and long-term use; in turn, disposable elements are best suited for rare, occasional use.
Battery in set
The number of batteries supplied with the respective tool (see "Power Source"). Also, this paragraph may indicate the presence of a built-in battery.
The most popular configuration option with a battery nowadays is 2 batteries. This provides additional benefits that are especially useful for long-term continuous use of the tool. So, when the charge of one battery is exhausted, you can quickly change it to another; while one battery is in use, the other can be charged. This minimizes or eliminates interruptions in charging. Some tools for the same reasons can be equipped with three batteries, however, such sets are much less common, since they are more expensive and do not have fundamental advantages. Single battery kits are also not particularly common: these are mostly entry-level tools designed for small amounts of work, when charging breaks are quite acceptable.
In addition, quite a few modern cordless tools come without batteries. This configuration assumes that the user himself will purchase batteries at his discretion (many models are compatible with several brands of batteries at once). In addition, this option may come in handy in case the battery is already on the farm. This happens quite often, since many well-known manufacturers use universal bat...teries suitable for different types of branded power tools. So a battery, for example, from a previously purchased jigsaw or grinder may well be compatible with a screwdriver from the same company.
As for non-removable batteries, this is a rather rare and specific option. Such tools are as compact as possible, but the batteries themselves cannot be quickly changed — so you will inevitably have to take breaks for charging during work. Therefore, this method of supply is typical for low-power tools — mainly screwdrivers (see "Device"). In them, small size is more important than a long period of continuous operation, in addition, a low capacity allows you to achieve good battery life even with small sizes (and, accordingly, capacity) of batteries.
The most popular configuration option with a battery nowadays is 2 batteries. This provides additional benefits that are especially useful for long-term continuous use of the tool. So, when the charge of one battery is exhausted, you can quickly change it to another; while one battery is in use, the other can be charged. This minimizes or eliminates interruptions in charging. Some tools for the same reasons can be equipped with three batteries, however, such sets are much less common, since they are more expensive and do not have fundamental advantages. Single battery kits are also not particularly common: these are mostly entry-level tools designed for small amounts of work, when charging breaks are quite acceptable.
In addition, quite a few modern cordless tools come without batteries. This configuration assumes that the user himself will purchase batteries at his discretion (many models are compatible with several brands of batteries at once). In addition, this option may come in handy in case the battery is already on the farm. This happens quite often, since many well-known manufacturers use universal bat...teries suitable for different types of branded power tools. So a battery, for example, from a previously purchased jigsaw or grinder may well be compatible with a screwdriver from the same company.
As for non-removable batteries, this is a rather rare and specific option. Such tools are as compact as possible, but the batteries themselves cannot be quickly changed — so you will inevitably have to take breaks for charging during work. Therefore, this method of supply is typical for low-power tools — mainly screwdrivers (see "Device"). In them, small size is more important than a long period of continuous operation, in addition, a low capacity allows you to achieve good battery life even with small sizes (and, accordingly, capacity) of batteries.
Battery platform
The name of the battery platform supported by the device. A single battery platform is used to combine various power tools of the same brand into one line (screwdriver, grinder, circular saw, etc.). Devices on the same platform use interchangeable batteries and chargers. Thanks to this, for example, there is no need to select a battery for each individual model of a power tool, because one purchased as a spare battery can be used in various power tools, depending on the situation or as needed. Batteries of the same platform basically differ from each other except perhaps in capacity.
Battery voltage
Rated battery voltage for which the cordless tool is designed (see "Power Source").
Manufacturers select the battery voltage taking into account the performance characteristics of the tool and the power supply required to achieve these characteristics. In fact, this means that most often this parameter can be ignored at all when choosing. The only exceptions are some specific situations — for example, if the "household" already has a battery of the same company and you want to evaluate its compatibility with the selected model, if the selected tool is supplied without a battery and you want to immediately order a power source for it, or for accurate comparison of batteries by capacity (see below for more details). But after the purchase, the voltage data can also be useful for finding chargers in addition to or to replace the "native" charger.
As for specific values, in many models the voltage does not exceed 10 V — this is often quite enough. However, much more popular options are 11 to 15 V and 16 to 20 V. There are also higher voltages, but much less frequently.
Manufacturers select the battery voltage taking into account the performance characteristics of the tool and the power supply required to achieve these characteristics. In fact, this means that most often this parameter can be ignored at all when choosing. The only exceptions are some specific situations — for example, if the "household" already has a battery of the same company and you want to evaluate its compatibility with the selected model, if the selected tool is supplied without a battery and you want to immediately order a power source for it, or for accurate comparison of batteries by capacity (see below for more details). But after the purchase, the voltage data can also be useful for finding chargers in addition to or to replace the "native" charger.
As for specific values, in many models the voltage does not exceed 10 V — this is often quite enough. However, much more popular options are 11 to 15 V and 16 to 20 V. There are also higher voltages, but much less frequently.
Battery type
The type of battery installed in the battery-powered tool (see "Power Source").
— Ni-Cd(nickel-cadmium). The most "old" option found in modern power tools. It is distinguished by high reliability, resistance to temperature extremes and good charging speed even with high capacity (which is important, given the "voracity" of the power tool). The main disadvantage of this type of batteries can be called a pronounced "memory effect" — a decrease in battery capacity if it is set for charging without being completely discharged. In addition, Ni-Cd cells are considered environmentally unsafe. Nevertheless, they are still widely used in tools — not least due to their low cost with decent performance.
— Ni-Mh(nickel-metal hydride). Such batteries were created as a development of the nickel-cadmium batteries described above. Retaining all the main advantages of their predecessors, they are at the same time devoid of most of the shortcomings — in particular, they are practically not subject to the memory effect. Of the own disadvantages of this option, it is worth mentioning a slightly lower durability and higher cost than the original Ni-Cd.
Ni-Zn. Nickel-zinc batteries are the next evolutionary step after nickel-metal hydride. They have no memory effect, have lower self-discharge rates (compared to Ni-Mh) and extremely low internal resistance, which makes...it possible to charge the battery at an accelerated pace using high current. At the same time, Ni-Zn batteries are sensitive to deep discharge and overcharging.
— Li-Ion(lithium-ion). A type of battery originally developed for use in portable devices; however, with the development of Li-Ion technology, it has also been used in power tools. The main advantage of such batteries in this case can be called a high capacity with small dimensions and weight. It is also worth noting that they are not subject to the memory effect and are able to charge quite quickly. On the other hand, this option is not without its drawbacks — this is, first of all, sensitivity to too low or elevated temperatures, as well as a high price.
Note that the tool may allow the use of batteries of a different type — for example, replacing a Ni-Mh battery with a more advanced Li-Ion. However, such a possibility must be explicitly stated in the documentation, otherwise normal performance is not guaranteed (and in the worst case, even breakdowns and fires are possible).
— Ni-Cd(nickel-cadmium). The most "old" option found in modern power tools. It is distinguished by high reliability, resistance to temperature extremes and good charging speed even with high capacity (which is important, given the "voracity" of the power tool). The main disadvantage of this type of batteries can be called a pronounced "memory effect" — a decrease in battery capacity if it is set for charging without being completely discharged. In addition, Ni-Cd cells are considered environmentally unsafe. Nevertheless, they are still widely used in tools — not least due to their low cost with decent performance.
— Ni-Mh(nickel-metal hydride). Such batteries were created as a development of the nickel-cadmium batteries described above. Retaining all the main advantages of their predecessors, they are at the same time devoid of most of the shortcomings — in particular, they are practically not subject to the memory effect. Of the own disadvantages of this option, it is worth mentioning a slightly lower durability and higher cost than the original Ni-Cd.
Ni-Zn. Nickel-zinc batteries are the next evolutionary step after nickel-metal hydride. They have no memory effect, have lower self-discharge rates (compared to Ni-Mh) and extremely low internal resistance, which makes...it possible to charge the battery at an accelerated pace using high current. At the same time, Ni-Zn batteries are sensitive to deep discharge and overcharging.
— Li-Ion(lithium-ion). A type of battery originally developed for use in portable devices; however, with the development of Li-Ion technology, it has also been used in power tools. The main advantage of such batteries in this case can be called a high capacity with small dimensions and weight. It is also worth noting that they are not subject to the memory effect and are able to charge quite quickly. On the other hand, this option is not without its drawbacks — this is, first of all, sensitivity to too low or elevated temperatures, as well as a high price.
Note that the tool may allow the use of batteries of a different type — for example, replacing a Ni-Mh battery with a more advanced Li-Ion. However, such a possibility must be explicitly stated in the documentation, otherwise normal performance is not guaranteed (and in the worst case, even breakdowns and fires are possible).
Battery capacity
The capacity of the battery supplied with the respective tool (see "Power Source"). The most modest capacity values in modern power tools do not even reach 1 Ah, such batteries are found mainly among electric screwdrivers(see "Device"). And in powerful professional models there are batteries for 3 – 4 Ah and even more.
Theoretically, the higher the capacity, the longer the tool will be able to work on a single battery charge. However, in fact, things are far from being so clear cut. First, the ampere-hour is a fairly specific unit; its features are such that only batteries with the same voltage can be directly compared by the number of ampere-hours. With a difference in voltage, you need to convert the capacitance to watt-hours and use them for comparison. Secondly, the actual battery life of the tool depends not only on the properties of the battery, but also on the power consumption and other performance characteristics. Thus, it is possible to compare different models in terms of battery capacity only with the same supply voltage and similar capabilities.
Theoretically, the higher the capacity, the longer the tool will be able to work on a single battery charge. However, in fact, things are far from being so clear cut. First, the ampere-hour is a fairly specific unit; its features are such that only batteries with the same voltage can be directly compared by the number of ampere-hours. With a difference in voltage, you need to convert the capacitance to watt-hours and use them for comparison. Secondly, the actual battery life of the tool depends not only on the properties of the battery, but also on the power consumption and other performance characteristics. Thus, it is possible to compare different models in terms of battery capacity only with the same supply voltage and similar capabilities.
Battery type
The model of a standard battery allows you to find out its characteristics in more detail, and also helps you understand what devices it is like and which one should be purchased in case of a replacement due to a malfunction or, if necessary, buy another similar one.
Compatible batteries
Battery models compatible with the tool.
When choosing a tool, this information is relevant mainly for models without a battery in the kit (see "Complete battery"). For tools that come with batteries, the battery model is more of a reference—it's mostly "for the future" if a spare or replacement battery is needed. However, this data can also be useful in the selection process — for example, to assess compatibility with an existing battery on the farm, or to find detailed data on compatible batteries and determine how they meet your requirements (in particular, there are formulas that allow you to determine the time of continuous operation from a specific battery; these formulas can be found in special sources).
When choosing a tool, this information is relevant mainly for models without a battery in the kit (see "Complete battery"). For tools that come with batteries, the battery model is more of a reference—it's mostly "for the future" if a spare or replacement battery is needed. However, this data can also be useful in the selection process — for example, to assess compatibility with an existing battery on the farm, or to find detailed data on compatible batteries and determine how they meet your requirements (in particular, there are formulas that allow you to determine the time of continuous operation from a specific battery; these formulas can be found in special sources).
Charging time
The time to fully charge the battery that the tool is equipped with from a standard charger (when using other batteries or a “non-native” charger, this time may vary both in one direction and in the other).
For cordless tools in general, see "Power Source". And charging time data gives you an idea of how you'll need to organize your workflow and how long breaks you'll need to charge your batteries. The specific duration of the process will depend both on the capacity of the battery (ceteris paribus, a more capacious model takes longer to charge), and on the technologies used by the manufacturer that increase charging efficiency. However, in general, it is customary to refer to tools with a good charging speed as models where this procedure takes no more than 45 minutes.
We also note that the specific meaning of this parameter also depends on the number of batteries in the kit. Recall that there are often several of them at once (see "Complete battery"), and while one battery is working, the rest can be charged. This allows you to reduce interruptions to a minimum, and even completely do without them. But if there is only one battery, charging breaks will inevitably be required in full. This is especially true for tools with a built-in power source (in models with replaceable batteries, the situation can be corrected by purchasing additional batteries).
For cordless tools in general, see "Power Source". And charging time data gives you an idea of how you'll need to organize your workflow and how long breaks you'll need to charge your batteries. The specific duration of the process will depend both on the capacity of the battery (ceteris paribus, a more capacious model takes longer to charge), and on the technologies used by the manufacturer that increase charging efficiency. However, in general, it is customary to refer to tools with a good charging speed as models where this procedure takes no more than 45 minutes.
We also note that the specific meaning of this parameter also depends on the number of batteries in the kit. Recall that there are often several of them at once (see "Complete battery"), and while one battery is working, the rest can be charged. This allows you to reduce interruptions to a minimum, and even completely do without them. But if there is only one battery, charging breaks will inevitably be required in full. This is especially true for tools with a built-in power source (in models with replaceable batteries, the situation can be corrected by purchasing additional batteries).
Power bank feature
Ability to operate the device in power bank mode. This mode is found only in models with their own batteries: it allows you to use the battery to charge / power a smartphone or other external gadget. Thus, a drill driver with a Power Bank function can play the role of an additional external battery, which is important in situations where it is not possible to charge a portable device in time.
Charging connector
The presence in the cordless tool (see "Power supply") of a standard connector for charging.
This feature is found mainly in low-power models with non-removable batteries (see "Complete battery"). Such a tool is usually equipped with an adapter cable from the charging connector to a standard USB. This allows you to use not only a standard device for such a battery, but also many other accessories — chargers for smartphones, tablets and other gadgets, universal adapters for sockets and car cigarette lighters, USB connectors on computers, laptops and other equipment, portable Power bank batteries, etc. P. Specifically, the connectors in power tools can be as follows:
— microUSB. One of the miniature versions of the USB connector, still popular in portable gadgets, despite the emergence of a more advanced USB-C. It has relatively modest capabilities (in particular, it is inferior to USB-C in terms of the maximum possible charging power), but this moment is rarely critical. At the same time, there are a great many cables and chargers for microUSB.
— USB-C. Relatively new type of USB connector. Like microUSB, it has a miniature size, but it has a more convenient two-way design and advanced features. In the case of a power tool, the main advantage of USB-C is the ability to provide fairly high charging power and reduce procedure time (although the specific power supported may vary — de...pending on both the charger and the tool itself). There are slightly fewer accessories for USB-C than for microUSB, but usually there are no problems finding them; and with the further development of this standard, the situation may change dramatically.
This feature is found mainly in low-power models with non-removable batteries (see "Complete battery"). Such a tool is usually equipped with an adapter cable from the charging connector to a standard USB. This allows you to use not only a standard device for such a battery, but also many other accessories — chargers for smartphones, tablets and other gadgets, universal adapters for sockets and car cigarette lighters, USB connectors on computers, laptops and other equipment, portable Power bank batteries, etc. P. Specifically, the connectors in power tools can be as follows:
— microUSB. One of the miniature versions of the USB connector, still popular in portable gadgets, despite the emergence of a more advanced USB-C. It has relatively modest capabilities (in particular, it is inferior to USB-C in terms of the maximum possible charging power), but this moment is rarely critical. At the same time, there are a great many cables and chargers for microUSB.
— USB-C. Relatively new type of USB connector. Like microUSB, it has a miniature size, but it has a more convenient two-way design and advanced features. In the case of a power tool, the main advantage of USB-C is the ability to provide fairly high charging power and reduce procedure time (although the specific power supported may vary — de...pending on both the charger and the tool itself). There are slightly fewer accessories for USB-C than for microUSB, but usually there are no problems finding them; and with the further development of this standard, the situation may change dramatically.
Powered by two batteries
The tool is powered by two batteries at once.
For battery models in general, see Power Supply. And this feature means that the tool is a heavy professional device with high torque, for which one standard battery is not enough. So if both high power and independence from networks are fundamentally important to you, perhaps the model with two batteries will be the best option.
For battery models in general, see Power Supply. And this feature means that the tool is a heavy professional device with high torque, for which one standard battery is not enough. So if both high power and independence from networks are fundamentally important to you, perhaps the model with two batteries will be the best option.
Charge level indicator
An indicator that signals the battery level in the corresponding tool (see "Power supply").
The device and capabilities of such a pointer can vary from an LED "light" that gives the simplest signals by changing colour and/or blinking frequency, to detailed data on the instrument's own display (see "Functions"). However, anyway , the charge level indicator makes it easier to monitor the state of the battery and reduces the likelihood of being with an “empty” battery at the wrong time.
The device and capabilities of such a pointer can vary from an LED "light" that gives the simplest signals by changing colour and/or blinking frequency, to detailed data on the instrument's own display (see "Functions"). However, anyway , the charge level indicator makes it easier to monitor the state of the battery and reduces the likelihood of being with an “empty” battery at the wrong time.
Battery mount
Method of attaching the battery to the tool.
— Clip. With this fixation, the battery is fully or partially inserted into the handle of the tool — like a clip (magazine) of a pistol, hence the name. This method is convenient in that when installing the battery, there is a minimum of unnecessary parts outside; and small low-power batteries can completely hide inside the case without affecting the dimensions of the tool. On the other hand, for powerful and capacious power supplies with significant dimensions and weight, the clip-on mounting method is poorly suited for a number of reasons. Therefore, this option is found much less often than sliders, and mainly among low-power instruments.
— Slider. This method involves the use of special guides — a kind of "sled" along which the battery moves during installation and removal; such "sledges" are usually placed at the bottom, at the end of the handle. The slider is suitable for batteries of almost any size and weight, including the most powerful and heavy batteries used in power tools. In addition, it does not have such severe restrictions on the shape of the battery as a clip-type mount. So most modern cordless tools use sliders, and for medium and high power units, this option is almost standard. Its disadvantages include perhaps the moment that the installed battery is located outside the tool and somewhat increases its dimensions. However, t...his point most often turns out to be unprincipled — especially for powerful and heavy devices that are initially quite large.
— Clip. With this fixation, the battery is fully or partially inserted into the handle of the tool — like a clip (magazine) of a pistol, hence the name. This method is convenient in that when installing the battery, there is a minimum of unnecessary parts outside; and small low-power batteries can completely hide inside the case without affecting the dimensions of the tool. On the other hand, for powerful and capacious power supplies with significant dimensions and weight, the clip-on mounting method is poorly suited for a number of reasons. Therefore, this option is found much less often than sliders, and mainly among low-power instruments.
— Slider. This method involves the use of special guides — a kind of "sled" along which the battery moves during installation and removal; such "sledges" are usually placed at the bottom, at the end of the handle. The slider is suitable for batteries of almost any size and weight, including the most powerful and heavy batteries used in power tools. In addition, it does not have such severe restrictions on the shape of the battery as a clip-type mount. So most modern cordless tools use sliders, and for medium and high power units, this option is almost standard. Its disadvantages include perhaps the moment that the installed battery is located outside the tool and somewhat increases its dimensions. However, t...his point most often turns out to be unprincipled — especially for powerful and heavy devices that are initially quite large.